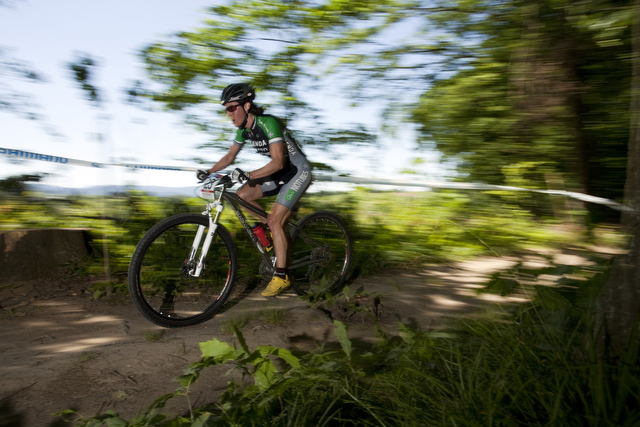
Seven was thrilled to welcome multiple-time national champion mountain bike racers and two-time Olympian Mary McConneloug and Mike Broderick to our Watertown offices yesterday. Mike and Mary are back from the Thirteenth Annual Alpentour Trophy and stopped by on their way to Mont Saint-Anne in Quebec for the second race in the 2011 UCI World Cup Series.
It was wonderful to see Mike and Mary, as always! They are like family and whenever they visit it feels like a reunion. Not only did we get a chance to catch up on their season so far, but we were able to have some productive discussions about Seven’s most recent offroad R&D endeavors; and it’s always helpful to get Mary’s and Mike’s astute insights.
Continue reading “Mary McConneloug & Mike Broderick Visit Seven Cycles”