Manufacturing
A Way of Thinking
"One bike. Yours." This isn't simply a slogan. It represents the heart of our philosophy about who we are and what we do. And nowhere is this philosophy more apparent than in our manufacturing.
At Seven, each craftsperson focuses on only one bike at a time. Yours.
Unlike most bikes, which are produced on an assembly line or in batches—destined for a warehouse or a shop's inventory—your Seven is created specifically for you. One machinist. One welder. One finisher. One bike. Yours. Literally.
Manufacturing Philosophy
Each frame is handcrafted one at a time, and built to order. Seven's meticulous machinists strive for 100 percent accuracy in every part they work on. Each frame undergoes five alignment checks on a solid granite surface plate throughout the welding process. Once aligned, the frame enters final machining, where it's reamed, faced and chased to the tightest tolerances in the industry. Each frame is shipped with a quality assurance card that is signed by the machinist, fabricator, welder, brazer, finisher, and painter who created it.
Seven Cycles aims to set the industry benchmark for quality and its continuous advancement. Our designers consistently strive to make the products lighter, more durable, and better performing. They cut costs and maximize profit by constantly improving the efficiency of the production process—never by cutting corners.
A Way of Doing
Frame building at Seven is both an art and a science, requiring a special harmony between creative enthusiasm and manufacturing discipline. However, there's no room for interpretation when it comes to quality. Each stage in our manufacturing—from materials selection to the application of the frame's finish—employs standards for precision unparalleled in the industry.
Consider our proprietary tube butting technologies. We hold the wall thickness variations to within 0.001"—less than the thickness of a human hair. Because even a 0.001" deviation can create a 5% difference in that tube's ride characteristics within the frame.
Then there's our obsession with frame alignment. Every Seven frame is subjected to no less than 50 alignment checks—28 in welding alone. Each is designed to guarantee the straightest, most accurate frame possible. It's no small effort to hold tolerances as tight as ±0.002" for the most critical measurements. (That's thinner than a sheet of paper.) But it's crucial to ensuring proper bike handling. Why do we go to such extremes? Creating the best possible ride characteristics is one reason. A passion to push the bounds of what's possible is another.
The Seven Process Methodology
The Seven Process Methodology (SPM™) is a unique production system we developed to allow us to build every Seven frame to order, with remarkable precision and efficiency. Each machinist, welder, and finisher works on only one frame at a time—from beginning to end—instilling a pride in workmanship and level of quality that could never be achieved with an assembly line or other traditional production systems.
Integral to SPM is our 100% Accuracy Initiative, which is a systematic approach to standardizing processes and tracking defects back to their root cause to address them at their source. These standards are born of our commitment to continuous improvement, ever driving us to seek out and develop systems to increase product excellence.
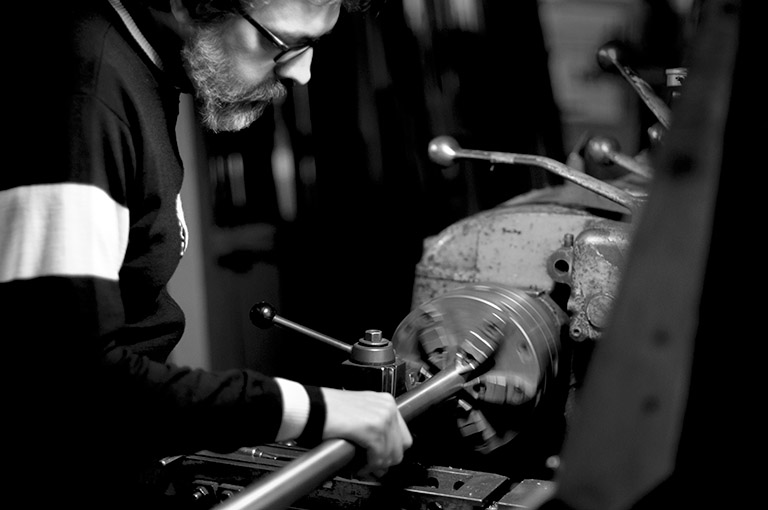
–Jim K., NJ
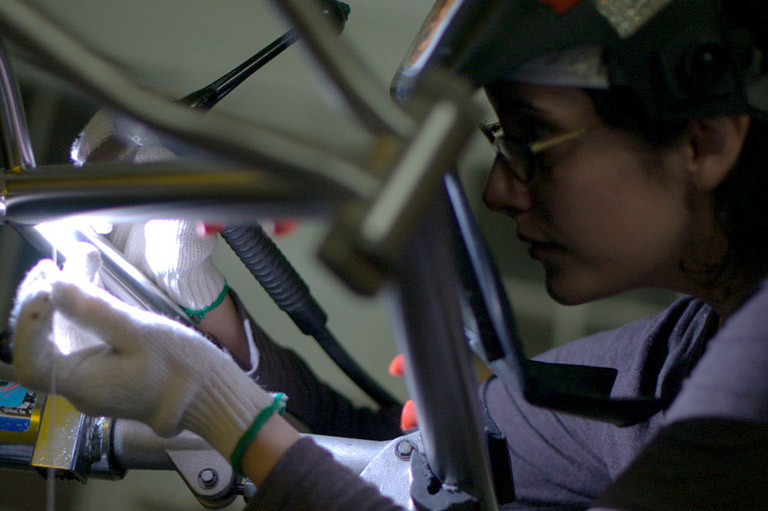
–Pro Cycling