If you’ve purchased a performance road carbon bike from a large brand in the past few years, the frame is probably designed for “Condition 1” riding constraints, along with a number of warranty implications.
Numerous large carbon brands use the following language in their owner’s manuals. Buried deep in the text that no one reads are a few paragraphs that should give pause. It’s odd that the text cannot be found with warranty information.
For context, Condition 1 is considered performance road riding. Condition 1 verbatim text:
You must understand that:
1) these types of bikes are intended to give an aggressive racer or competitive cyclist a performance advantage over a relatively short product life,
2) a less aggressive rider will enjoy longer frame life,
3) you are choosing light weight (shorter frame life) over more frame weight and a longer frame life,
4) you are choosing light weight over more dent resistant or rugged frames that weigh more.
These frames are likely to be damaged or broken in a crash. They are not designed to take abuse or be a rugged workhorse.
Would you buy a frame that had these usage constraints? Did you buy your high-end carbon bike with the expectation that these were some of the limitations of the bike?
What’s the tradeoff of fragility?
Seven doesn’t believe in building Condition 1 bike frames. Sure, a rider can maybe save 200 grams over a rough and tumble Seven frame in titanium or carbon. Fortunately, that 200 grams is virtually meaningless in real-world rider performance. Yes, cutting 200 grams will climb marginally faster. However, the bike descends more slowly, and, more importantly, does not handle nearly as well, thereby slowing the rider even more, or worse, causing a crash, as the pros do more and more each year.
Don’t chase grams. Instead, chase PRs with a bike that removes obstacles to handling, control, and the true source of bike speed.
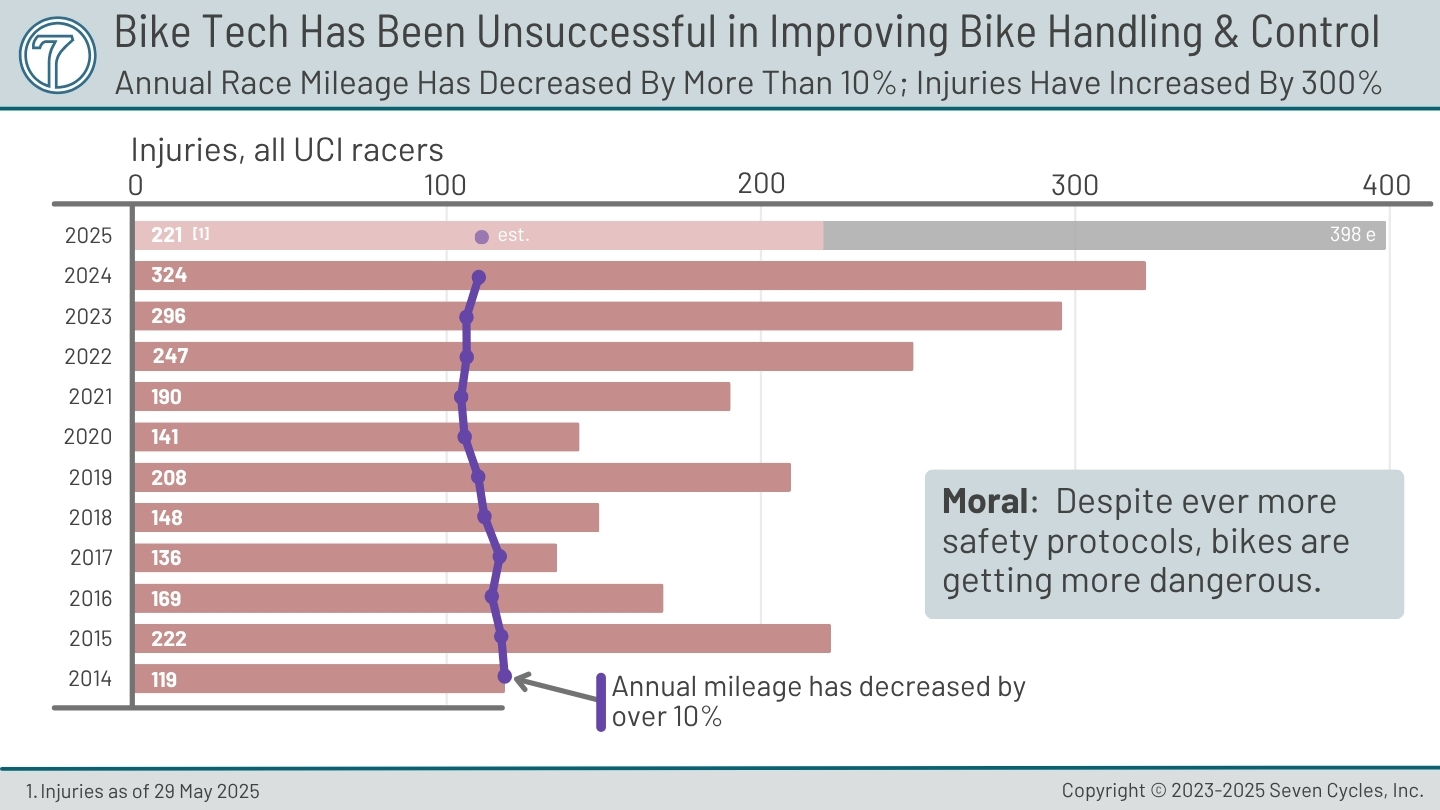