Gritty Nylox bristles whip over the titanium tube and brush off the discoloration left behind from welding. The sound isn’t deafening, but with three other frames being wheeled at the same time, it is pretty loud this afternoon. The final stage, before frames get wrapped up and shipped out, or in my case handed off, is my favorite to watch. Unlike a welder, whose hands move slowly and steadily, frame builders move about like dancers. Twirling around the stand as they flip, twist, and rotate the bike, their performance looks choreographed. Dan C. is working on my bike, but his recital isn’t a dance at all, in fact it’s one of the most arduous parts of fabrication. We call it “FINISHING.”
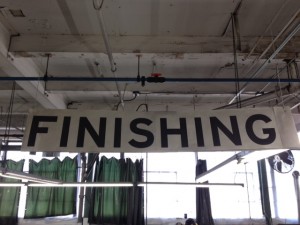
Before I caught up to him, Dan had already run my frame through the CNC machine where the bottom bracket was threaded, faced, and chamfered. In machining, the bottom bracket starts as a thick walled, round tube. When the down tube, seat tube, and chain stays are all welded on to it, the heat distorts the metal, microscopically, but enough that it’s no longer perfectly round. The thick tube wall is important because our CNC machine will bore through it, expanding the inner diameter to leave a perfectly round hole, which it can then thread. You can see the difference in wall thickness.
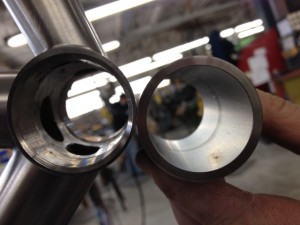
Dan had also faced and reamed the 44mm head tube so my Chris King InSet 7 headset will press in evenly. As an aside, the lathe that faces and reams head tubes is my favorite machine in the building. Who knows what it did before it came to Seven, but it looks old and tank like. I bet it weighs several tons. Head tube after head tube, it keeps working, just like new. Spin the crank and it goes round and round like a Record square taper bottom bracket. So cool.
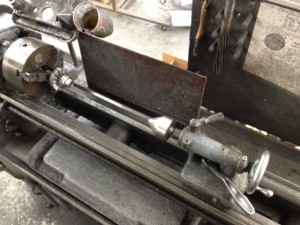
When those two steps were finished, Dan bonded in the seat tube insert, cut the seat top binder notch, and checked the frame’s alignment, making improvements where necessary.
By the time I got back to see how it was coming along, my bike was half way through the wheeling process.
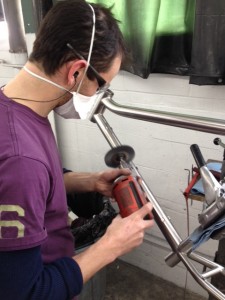
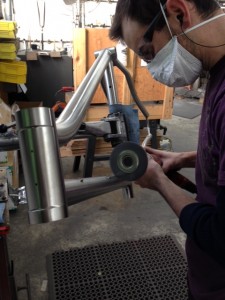
Once the main tubes have been wheeled, and the natural sheen of titanium comes through, he’ll exchange his drill for a ruddy strip of Scotch-Brite. The Scotch-Brite pad gives a uniform finish to the frame that can be replicated at home, at the end of the season, or whenever I want it to look like new.
When the frame passes Dan’s final, grueling, inspection, he’ll attach all of the small parts. The last step is to wipe down the frame with a light furniture polish.
Pretty soon my frame will be ready to build, and I will be bouncing off the walls.