The Big Ideas, as a series, is about this whole bike building project we embarked on in 1997 and the foundational ideas that make what we do possible. The first installment was about Single-Piece Flow (SPF). The second installment was about Just-in-Time manufacturing (JIT).
This week we explore the 5 Elements of Customization.
It is all well and good to tell someone you can build their ultimate bike, but if they don’t have the vocabulary to tell you what that bike should look like, you’re no closer to that bike existing than you were before you met them. The 5 Elements give riders a useful way to think about customization.
The 5 Elements are the language of Single-Piece Flow on the bike shop floor.
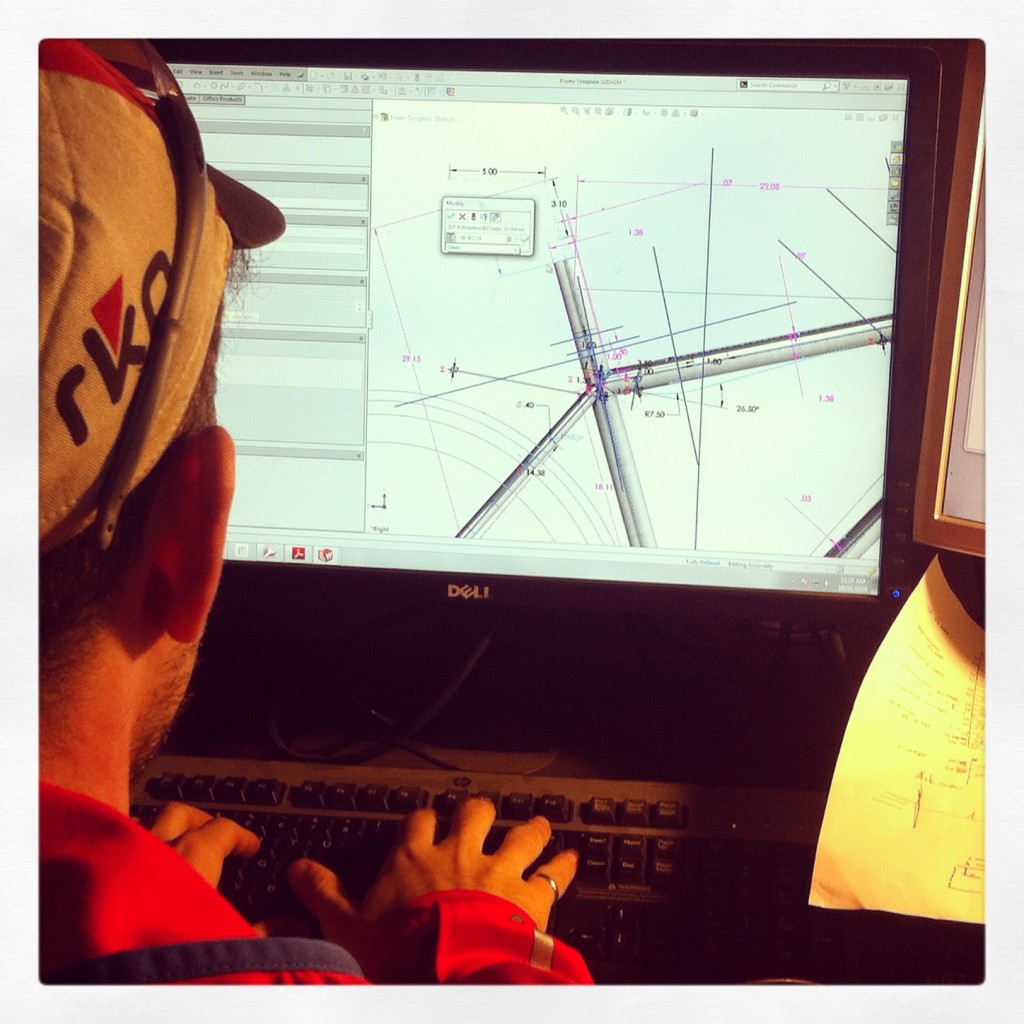
1) Fit & Geometry – Think of the upper half of the bike, the points where you touch the bike, saddle height, set back, reach, bar height. These are the angles and centimeters that address different riders’ size, proportions, age, style and health (injuries). We address these, at the shop, through a bike fitting, and then follow up with body measurements that allow us to consider that fit in terms of your new frame’s geometry.
2) Handling and Performance – Think of the lower half of the bike. This is where we fine tune for rider weight, comfort, handling and riding conditions. Bottom bracket drop, fork rake, chainstay length, all these things affect how the bike feels. If you tell us you want your bike to be stable or quick handling, we can produce those characteristics through fine tuning of handling and performance features.
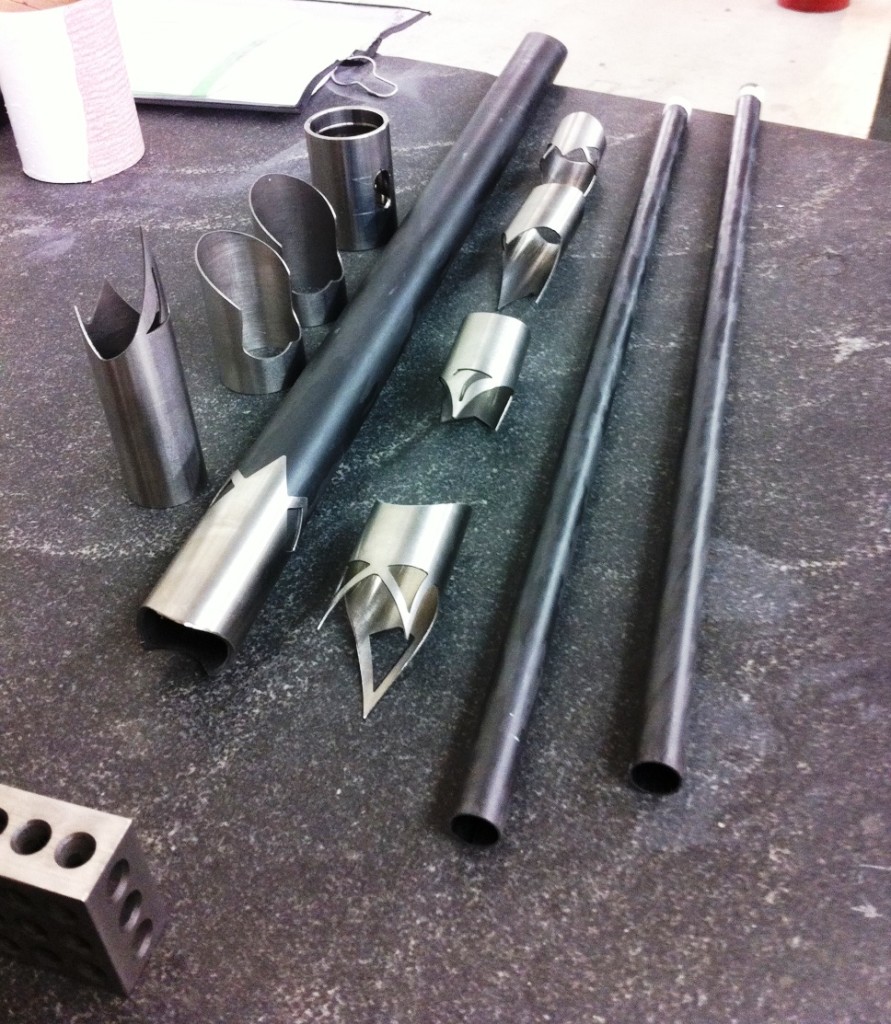
3) Tubing & Materials – We work in steel, titanium, and Ti/carbon mix. We start from the beginning when designing a bike for you, choosing a material that speaks to the kind of riding you do, then we go further, picking a tube set, in that material(s), that matches your specific preferences for stiffness and/or comfort, then we go further still, refining your rider-specific tube set through tube butting processes to accomplish the most personalized on-bike experience available from any custom builder, anywhere.
4) Options – Brake types, rack and fender mounts, decal colors and placement, paint, cable-routing, couplers, chain or belt drive component optimization, the configurations and permutations are close to infinite. This is how you dial the bike in. This is how you meet ALL your goals for your new bike, without compromise.
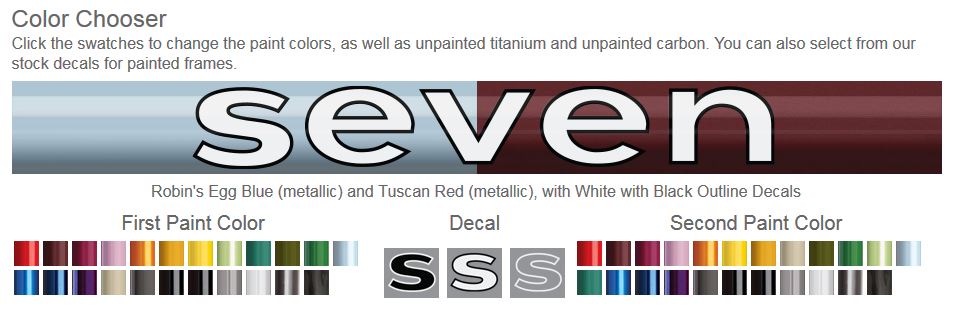
5)The Future – This is how we make our design as durable as our materials. We plan for the rider’s aspirations. Racing? Touring? Commuting? How does the bike age with the rider’s body? Is it adaptable? How do we keep the bike useful for the rest of the rider’s life?
You don’t have to be a bike designer to collaborate with us on the design of your new bike. You just need to be able to express your preferences in simple terms and let us map them onto the 5 Elements of Customization.