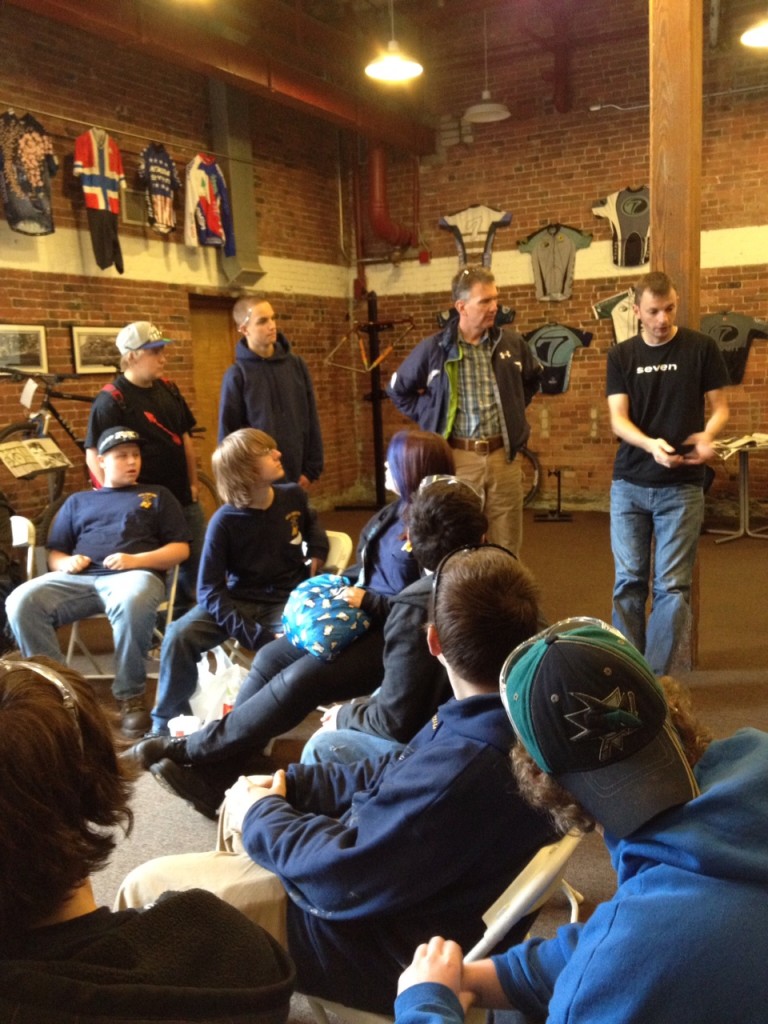
Neil, or rather Mr. Mansfield, used to work alongside Seven Cycles’ founders as a welder at Merlin Metalworks before moving on to become a top tier welding and metal fabrication teacher at the Assabet Valley Vocational Technical High School in Marlborough, MA. To help generate learning moments, Mr. Mansfield sets up field trips to show his class real world applications for the skills they learn throughout the school year. Today’s example was tube welding, and what better way to bring welding to life than showing his class what he did more than twenty years ago?
One way to create buzz at Seven is to drop a bus load of students into our showroom. The entire factory was crackling with energy.
Before splitting into groups, we opened the floor to questions, and were inundated:
- How much is that bike?
- How much does it weigh?
- Do you make BMX bikes?
- How long does it take to make one?
- What are they made out of?
- Do you weld?
- Why not?
- How long do they last?
- Are they strong?
- What happens if you crash?
- Is titanium better than steel?
- What if I wanted a BMX bike, then could you make one?
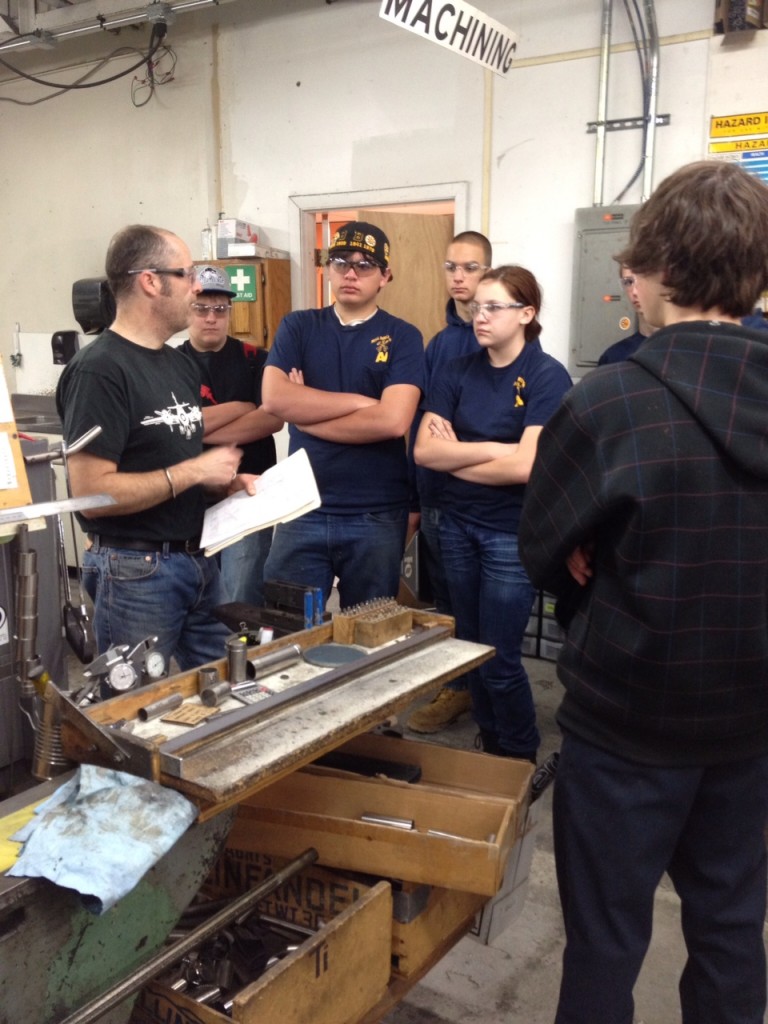
Once their questions were answered we headed out to the production floor for the real fun. Starting in machining we covered the basics of tube preparation, cutting, coping, bending, curving, and squishing. As is the case year after year, Neil’s classes are always more mature than their age would suggest and this class was no different. Their questions honed in on the craft and harkened back to things they had studied and practiced in their classrooms.
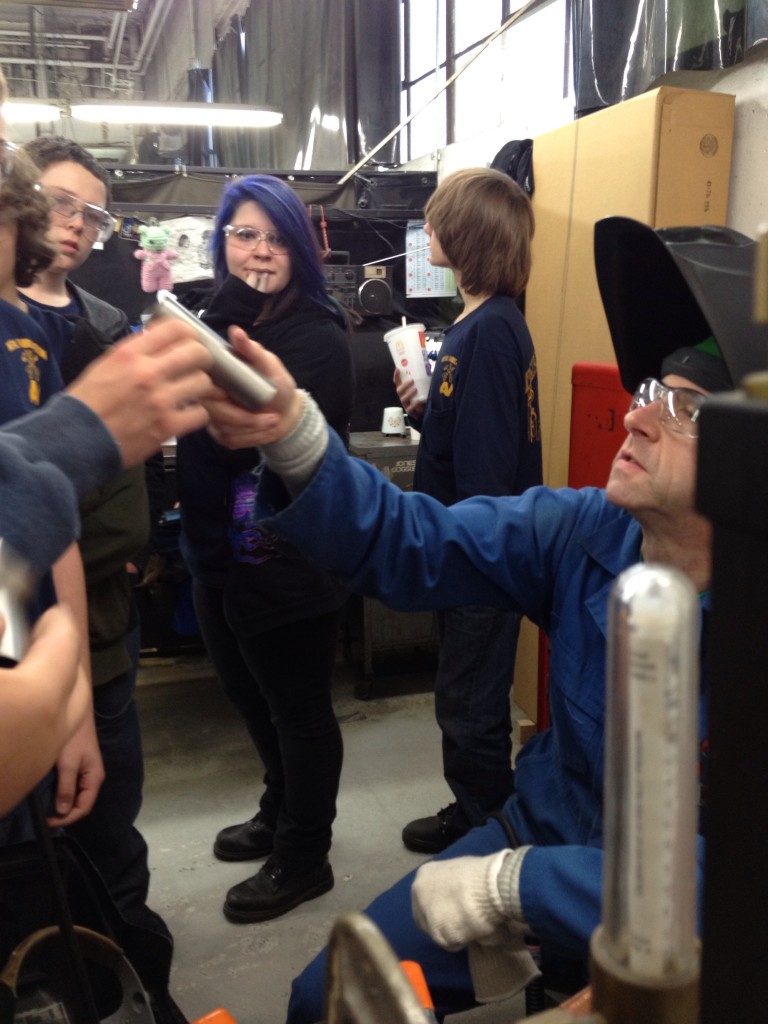
The highlight of every tour, for both the me and the students, is when we get to Tim Delaney’s welding bench. Not only is Tim an encyclopedia of welding knowledge, he is also a natural educator. When he speaks, people listen with interest and enthusiasm, and the rapport is instantaneous. I’m certain that the students’ interest in Seven’s welding process had a lot to do with it as well. They pummeled Tim with questions, donned welding masks, and watched as he showed them examples of what we do here at Seven. When the questions came to a close, we moved to final machining, then finishing, and finally to painting where Staci was working on a Diamas SL, which garnered some serious attention.
Wrapping up in the show room, Matt O’Keefe took some final questions on job inquiries, and positions for beginning welders. Needless to say, those of us over age 15 were exhausted by the end of the tour, in a good way, but the kids seemed to be ready for another go ’round. And lunch! We were really happy to have spent the morning with Mr. Mansfield and his smart, interesting, and very well-behaved students. We hope that someday, we can call one, or even a few of them colleagues.
-Karl B.