As you can imagine, at a company whose name is Seven, numbers play an immeasurable part in everything we do. The name Seven, just to get this out of the way first, is a product of our desire to build bikes to be ridden on the seven continents, a lucky number, a prime number, and even as a word, a symmetrical combination of letters that looks good on a down tube.
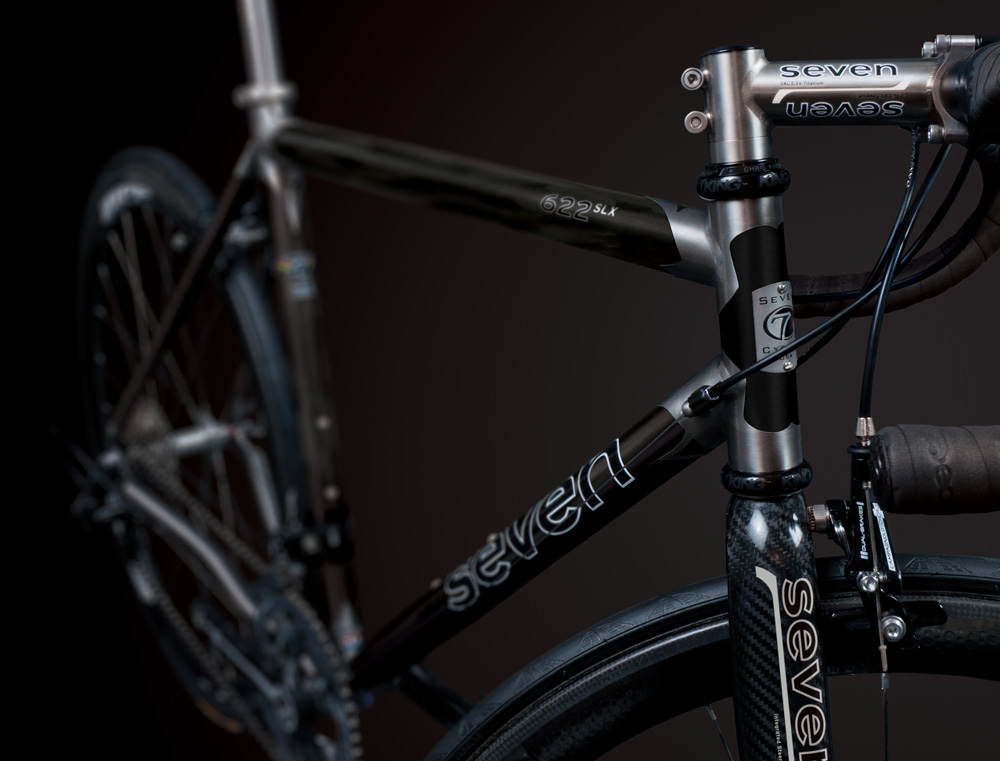
Taking a step backwards to six, the first number in the name of our category defining 622 SLX, we find carbon, the sixth element in the periodic table. Carbon fiber is the defining element of the 622 line of bikes. It brings elemental lightness to those bikes. High frequency vibration, radiating up from the road or trail, disappear between the fibers.
Now jump forward to twenty-two in that same table, titanium, the metal that launched our bike building careers. Five times the strength of steel at the same weight, titanium moves with a rider like nothing else. It flexes and returns microscopically, soaking up the lower frequency jolts that push beyond carbon fibers range. Titanium smooths the ride, keeps your tires connected, spares your muscles. It won’t rust. It holds a shine like little else.
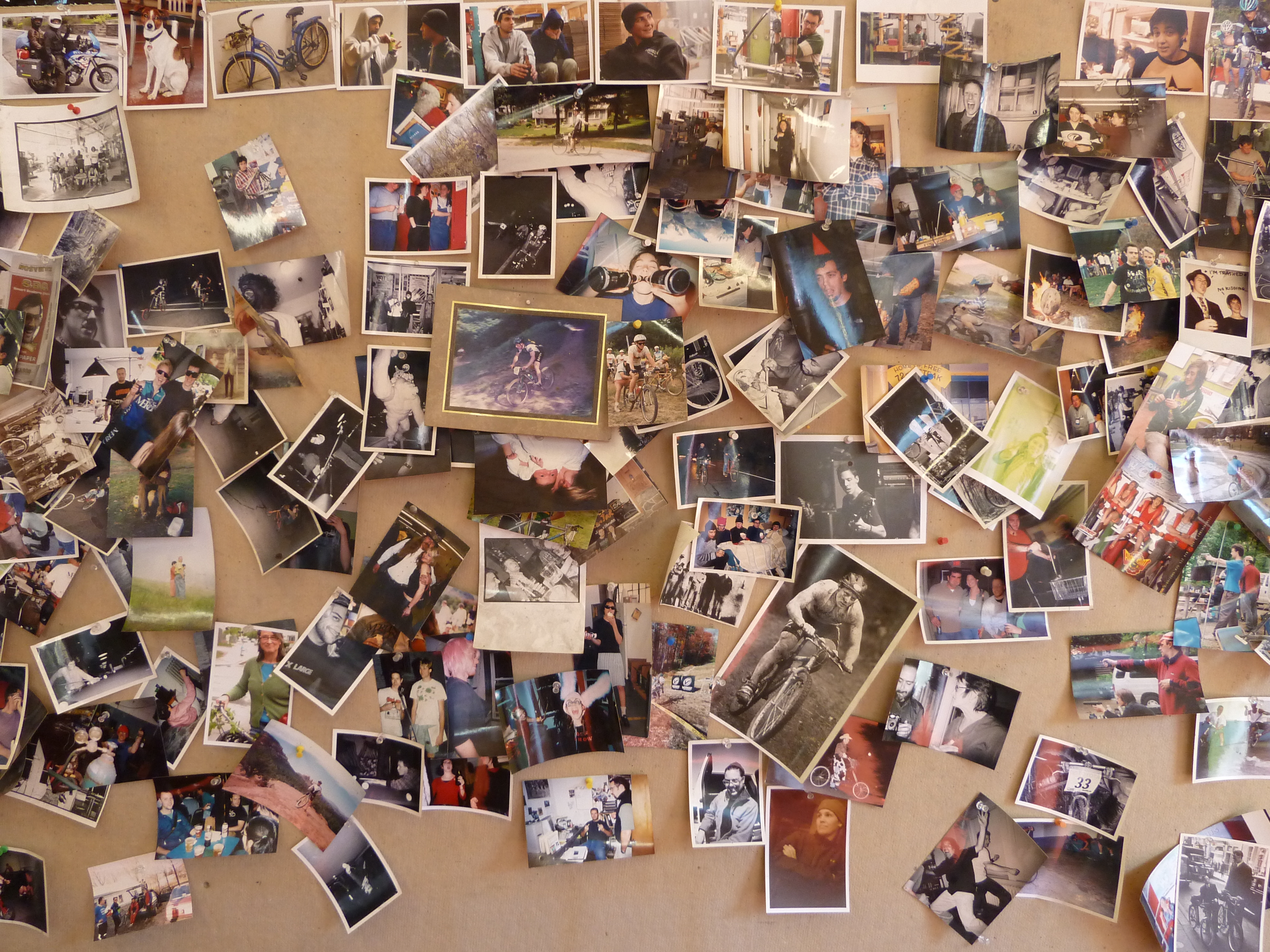
Nineteen is another prime number. Nineteen is the number of years Seven has been building and delivering bikes. Our second full decade is there on the horizon. And, with apologies, we are primed to do our best work. This year’s R&D effort will produce a slew of new products, new bikes, new forks, new frame components. We have already begun planning limited editions for our anniversary, already begun gathering the ideas that have been developing over those decades.
There are so many more numbers, too. Too many to call out, the lengths and angles of every rider-specific frame we’ve designed, more than 30,000 of them, the number of bike and component companies we’ve partnered with, the hundreds of bike builders we’ve been fortunate enough to train and learn from in return, and of course, all the riders, many of them with two, three and more bikes they asked us to build for them, maybe the most important number of all.