by Charles Manantan
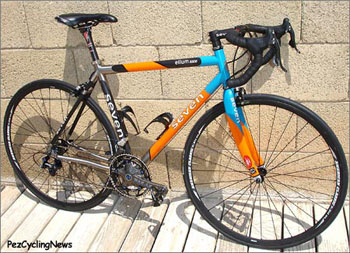
Housed in a modern little complex tucked away in an older section of Watertown Mass, Seven Cycles turns out their version of custom Titanium and Carbon cycles. Founded 8 years ago by Rob Vandermark and a few close associates, Seven has grown into one of the most recognized “it” brands in Cycling.
They are such an “It” brand that my spoiled bike slathered butt would be willing to leave 70 degree, no arm warmers training days in Phoenix to fly into this!
I absolutely hate cold weather and always thought that I would avoid it at all costs. Turns out that “all costs” actually ends some place shy of 5 grand, so off I flew. I get off the plane and, after a bit of “fun” (my damn hand actually froze stuck to the door handle of the car!) hit the Hotel and parked up for the night. Next morning it’s out to the car, where I wait for 10 minutes for the half-inch of crap on the windows to melt and it’s off to Seven. I get outta the car, struggling to see past my breath (breath will actually blow back and freeze to your face if you move fast enough) while sliding down an icy hill and through the parking lot. The whole time I am thinking, “It’s a frikin’ Seven for crying out loud, just suck it up and nail down a Dream Bike!” Then I walk through the door and see this:
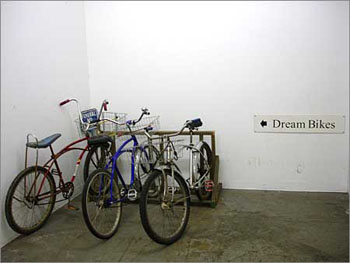
Of course it got a little better when I get walked to the waiting area and found a sample of the bike we would have made for us.
Mr. Seven
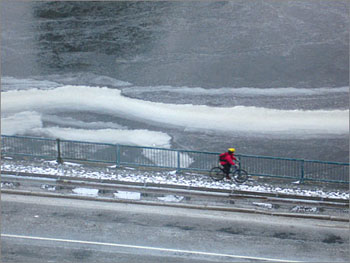
Seven’s history goes back quite a ways past its relatively short history. It goes back nearly to the roots of Merlin in it’s pre-sold and sold again days before becoming a part of today’s American Bicycle Group (who are Preownedbikes.com / Merlin / Litespeed / QuitanaRoo / Tomac). Rob Vandermark was actually the first full time employee hired by the founders of Merlin. He had been working at a bicycle shop for a few years (he had to find a way to pay for the gear he needed to keep up with his brother) while getting through school on a scholarship as a sculpting major. His emphasis was on representational Bronze, so he had some art world experience with welding, casting and machining, but admitted that he “never thought it would come in handy”
A friend of Rob’s found an ad in the newspaper from a small frame builder working in Titanium and Rob thought he’d give it a look. Funny that he was also thinking that “Ti isn’t a bike material” Once at the interview, he thought “this is crazy, what am I doing here”. But he kept his thoughts to himself well enough to get the job. And as a metal sculptor with artisan skills and a love of bikes, he was promptly put to work.
… As the official company bike packing newspaper crumpler.
“I almost didn’t come back the next day” Rob says, but he’s glad he did as he was with Merlin for eleven more years helping to develop Ti technology for cycling as well as the magic brand that Merlin would become.
But the Bicycle game is what it is and with a few changes in ownership the new management wanted to focus on how the company looked on paper. While business is business and Rob has a lot of respect for the folks at Merlin, he wanted to concentrate on developing a high end, custom / customer focused product. And so, Seven cycles was born.
In it’s eighth year, Seven has become a world recognized custom house. While that’s a young company in the cycling world, Rob has been working with some of the staff at Seven for more than 17 years and they employ a couple of hundred years of Ti bike experience and a bazillion years in the cycling field for their staff. At Seven, extremely good building talent and a bit more modern thought process has done more than just create a hell of a bike. It has also spawned a bit different custom process where Sevens staff take a bit more active roll in working directly with the customer to make sure that they understand how best to apply the tools and materials to what an individual will need in their bike.
Note: The place is full of really skinny smart people that ride (the guy that welded my frame is probably sporting a backwards Molteni cap right now) and I got the feeling that they were as excited about the bike as I was.
Fitter Up!
It was an incredibly satisfying when we got the call from Seven simply to say “Nice job” on the details of a bike test that we had just finished. Of course it was even more satisfying to have them call us later with the opportunity to have a frame and fork.
And rather than having the process handled like a journo schmoozing (not that I qualify as a journalist), red carpet super fit, we didn’t go see em till very late in the process. We got our bike the same way you would (we were even offered the chance to do it with someone out of town so that we could be sure that Seven’s service works everywhere).
The fit process is a little different with Seven. It is less dependent on a fitter (which I found strange and disturbing at first). Seven do ask that you get the help of someone to help you take the measurements for your body and your current bike, and they have a very easy (and complete) set of dimensions they look for.
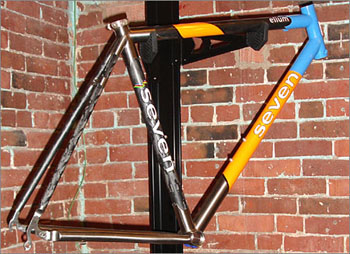
Once they have your tale-of-the-tape, they use their personal interview process and a top secret formula ( based on a 12-year study of ergonomics, biomechanics, and kinesiology, as well as the overall state of bike fit ) to decide what dimensions your frame should be, while also taking component choices in to consideration (including seat set-back, crank length and stem rise and length, bar reach, etc.).
Screw em!
They also ask for measurements of your old bike (as a point of reference), and they ask you several questions about what you do and don’t like in your current ride. Now we’re nobodies fool (er OK, few people’s fool) and they knew that I was in love with my last bike (another custom fit dreamer). So not only did I ask for a bike that would behave differently than the bike they knew I loved, I gave em a “modified” version of my bikes measures in order to see what their pre-production suggested measurements would be.
In short, I lied to try and screw em up.
Now remember that frame geometry can change dramatically within your fit. Your hands, feet and butt can remain in the same place while the angles between can be way different.
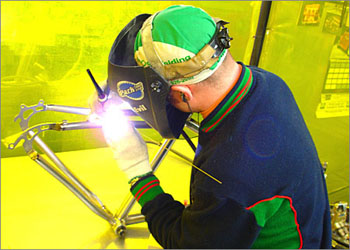
I already had a perfect fit on a bike with an emphasis on being super stable, relaxed and comfortable (a distance eater that would respond when asked). With that in mind, I asked Seven to build something quicker steering and stiff as a first, second (and third) priority (why not have a custom fit dreamer with another focus eh?). I did give Seven my accurate body measures but did not give them an accurate accounting of where my contact points were on the other bike. Instead I gave them a longer saddle to bar measurement and also screwed up my seat set back.
Sonsabitches found em both.
Zac, my contact and interviewer at Seven, sounded a little worried (much to my sick pleasure) as he started to tell me that the (false) fit I raved about wasn’t what Seven had come up with. “I know you really like what you have now, but I’m not sure that you have the optimum fit, and we were wondering if you might try what we’ve come up with” was how he delicately put it:
I said “sure, what did you come up with?”
After applying my measurements and bike desires to their formula, they corrected my “altered” seat setback to exactly the same spot my current (good) fit dictated, and they corrected the reach to the bars to within 5mm… Not exact enough? Well another variable is that I had spec’d a different handlebar for the Seven and the reach to the hoods was 2.5mm toward the suggested Seven measurement. So they came within one quarter of a stem size of dead on. The saddle height they suggested was also a virtual match…
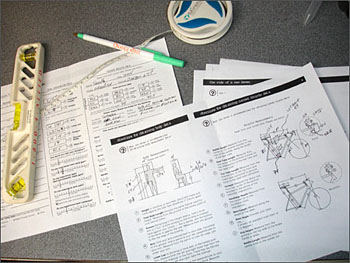
Long story long (sorry!) they did a better job of fitting me than I thought was possible without seeing me on a bike. Maybe that was a fluke, but I have not seen a 4 part fit fluke before now! I would also say that you need to be extremely honest about your performance, flexibility, fitness level and desires with them, as they take it all in to consideration.
Note that I love how Seven found my fibs, but I am physically fit and relatively well conditioned with no major problems and no significant fit conditions. I would suggest that you get with a highly qualified fitter if you have special conditions and also discuss them with Seven when ordering, just to make sure that the information you give is acquired, handled and received properly.
So What’d We Get?
Seven’s top-dog Elium Race.
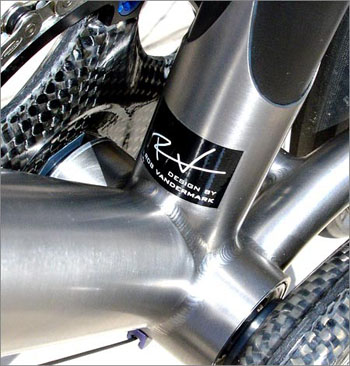
As frames go, it’s obviously a sweet bike. It was made sweeter by a few called in favors. Not only is the frame and fork a top spec, but Cycling Innovations sent us a one of a kind Crank set From ROI Bike special for this bike as well as some other select hardware From Tiso.
you’ll see a review of their stuff shortly
Schmolke sent us their Uber-bars, a sweet stem cap as well as a custom seat post. We’ll do a review of their stuff too.
And we had Reynolds new Carbon Mid V wheels as well as a super new set of Magnesium clinchers from American Classic. Stopped by a set of custom etched Pez Tech edition Zero Gravity brakes.
And Seven’s house stem (with Ti bolt upgrade) is no slouch. So nice that we stayed with it rather than spending money on something that didn’t have opposing force rear bolts and a “pull” rather than “push” face plate.
All this made for a disgustingly nice bike that will have the folks in forums ranting away (much to my personal pleasure mind you?) at our acknowledgement that this is nice kit, as if they wouldn’t take it.
Of course we did use the house wheel sets and saddle, and remounted our standard test bars so that we give you as much of a relative “bike” review as possible, but I will admit that I was as tainted as is humanly possible riding this thing in it’s photo-build.
Oh yeah: The Bike!
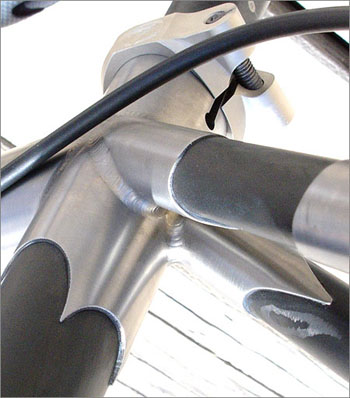
Dealing with one of the better custom houses is a great time to remind you of the old saying “be careful what you ask for. You might get it”. Again, your honesty in the interview process is critical with Seven. They have over 25 Ti tube sizes from the mill to chose from (then they custom butt the Ti for your ride). They also have a rack of different Carbon tubes to run.
The result of this mountain of available tube tuning is that I asked for a bike that focused on quickness in handling and stiffness under force. They handed me just that.
Probably the easiest place to see the focus of this bike on the stiffness side is in the Chain stays. These are the largest I have ever seen on a bike my size.
note the stays are larger than the fully inflated 21 tire. The green mark is where the tire is the same distance from the camera as the stays
The Chain Stays in the photo above were the same size as a massive set of stays on a BMX bike that the shop was working on as I came to look at my frame. There is virtually no wheel twisting the dropouts allowed by these tree trunks (I did break a spoke with the load I put to a wheel though!).
The bottom bracket looked like a bottom bracket. It holds the chain stays out wide and had welds that were so smooth and uniform that they looked like they were drawn on rather than welded.
Keep in mind that (within reason) a twisty bottom bracket area in and of it’s self doesn’t rob you of too much power. As you force a frame to twist as you press down, it’s also rotating and pushing your “up-leg” up (and both forces are driving the chain). You do get a loose “feeling” with a sloppy bottom bracket though, and the play also promotes side force on the tire. That “woosh-woosh” you hear as you stand and pound the cranks is made by the tires pressing sideways and the further your frame flexes to the side, the more power is lost scrubbing tires side to side. Some folks think as much power is lost in nervous energy created as the rider gets the feeling that a lot of power is being wasted or that he / she isn’t stable: and more flex is probably coming from your wheels when you’re riding most of today’s high end stuff. All that said, the bottom end of the Seven has virtually no twist at all. The feeling is incredibly satisfying stomping the pedals.
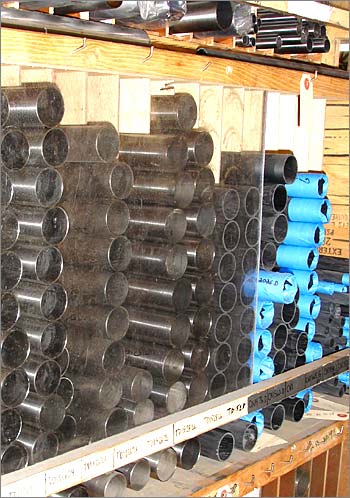
Note It’s important to note that all Ti is not the same. Nor are all welders. Done right, it’s great stuff. Done wrong (too slowly, in an unclean environment, wrong settings with the equipment, unevenly). Ti can be crap. That’s part of the reason it takes a year of training and apprenticeship to weld frames at Seven.
The down tube didn’t look as oversized relative to other bikes as the Chain stays did. Rather than going with a super fat tube, Seven kept things looking a little conservative and simply didn’t remove as much material from the tube walls (strategically removing material is what “butting” basically is). There are certainly sloppy Ti bikes out there, as some manufacturers pull too much material from a Ti bike to shave weight. Seven will pull just the amount of material out that gives you what you ask, bouncy or stiff, your choice.
The easiest bling to see on the Seven is in the funky weave in the Carbon tubes. It’s the first thing people ask about, as it’s obviously carbon and very unique. It’s multi directional carbon and once finished, the layers show up in what I call “camo-fiber”. The top tube is made from the stuff so that it can be very light and also resist twisting.
The Seat tube is Carbon to help with vibration absorbing. Seven insert the carbon as far as possible in the lug and leave the bottom of the tube fairly thick at the BB insert (for stiffness). The carbon also runs all the way to the top, at which point it receives a composite insert to house the seat post (you can see it inside the clamp below).
note that the seat collar is well made with a big bolt that is so easy to tighten that you may not think it is as snug as it is, much to my “old” seat posts displeasure.
You’ll also notice, around the seat tube joint, the shape detail machined of the lug, as well as the weld uniformity (can you spot where the welder had to change directions?). Also note the shape and machining of the seat clamp. It’s a little detail, but the little details at this level all add up.
The Seat stays and bridge are a split system rather than a wishbone. Seven say that keeping them separated to the top prevents side flex better than a wishbone for a given weight. Seven also pioneered the carbon / ti thing with the Odonata back in the mid-late 90’s.
These stays are straight as a golf shaft rather than being bent. This along with those tree-trunk sized Chain stays add up to a rear end that holds the back wheel in line as good as anything I have ever ridden (Aluminum, Carbon or Ti!).
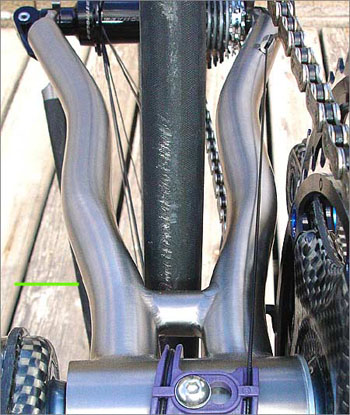
This stiff build spec mates up well with the fork Seven supplied. But then Seven’s fork should match well with darn near any lay out, as it comes in 18 different rakes designed to match character of an individual’s bike. The relationship of the fork to a frame set’s character and the balance of properties between the front and back wheels can’t be stressed enough. Sevens worked with Reynolds to create this huge range of forks and the result speaks volumes to Seven’s commitment to total ride performance. The fork mates with this frame and leaves me asking for nothing more than what I got. Side load handling, twist resistance and brake force resistance are absolutely top notch.
The Low-Down On Weight?
I hear people gripe about the weight of custom Ti / Carbon bikes on the market.
After having been on several (we actually have a couple more customs to publish after this) I can say that the feel and performance of lots of custom Ti only or Ti Carbon bikes, when done well, is great. You ride a bike, not a spec sheet after all.
Seven choose Ti down and Carbon up, and a large portion of the weight on this bike sits between the axles and not up high in your hands.
Green’s Carbon, Red’s Ti and the weight is pushed low-low.
Add the light bars, post, stem and brakes, and the weight that you can actually feel on the Elium is as good as any bike at any weight…
That said, it’s light anyway, as the photo build version is below the UCI minimum legal of 14.99 pounds. We were only under by a couple of grams, but this bike is sturdy from stem to QR’s, unlike some of the absolute foolishness that you see up for offer these day.
As weight restrictions go, my take on the UCI’s weight regulations is similar to Mr. Vandermark’s. Neither of us thinks that sticking million dollar athletes in the middle of a weight weenie-measuring contest is a good move. (Given the pathetic insurance that some riders get from teams, I would actually hate to see a workman get hurt even more than one of the stars.) And the UCI weight restriction hasn’t changed or prevented bicycle manufacturers development and concentration on weight at all. People are putting out lighter and lighter gear all the time. The UCI rule just means that riders can use fewer stupid parts on a bike (unless you’re sponsor does something like Cannondale a while back, who chose to add little weights to Simoni’s bike rather than performance).
Honestly, I am not sure the weight regulation hasn’t helped bike companies (and poor marketing folks) more than hurt them. Now manufacturers get to say “Our bike is illegal!” and leave that as a parts only benefit.
Anyway: With the weight being down low in this bike, it feels lighter than 14 and change. This coupled with the steeper geometry, shorter wheel base and super-light hoops, makes for a bike that drops in to corners faster than I was ready for! Flick-able is an understatement with the Elium Race.
What’s The difference?
If bikes were birds, my stable, comfortable, damn fast custom bike would be an Eagle. It gets up in the sky plenty quickly and is also a breath-taking swooping high speed descender. My QUICK-quick turning, quick accelerating damn fast custom Seven is more of a hummingbird.
And the hummingbird just got a beak full of RedBull!
I think “Go left” and don’t get to finish the thought. I think “left – right” and The Elium is already thinking 4 turns past that. I admit that part of this may be because I don’t think so gooder than sum people. But you could have a brain like Einstein and the reflexes of a young Sugar Ray Leonard and still not push the Seven past yawning at you.
Add the stiffness to the handling from a steeper geometry up front and you have an off the charts, slug-em-in-the-face-then-slam-the door-before-they-know-who-did-it Crit bike. This is a perfect toy to make wheel suckers life a living hell trying to stay lined up with your butt. Change of pace is also effortless and it matters not if you’re seated or standing.
Comfort was a secondary concern for me, as I thought I would give up quite a bit to get this kind of quickness, but the Seven soaks up road buzz very well. It translates big bumps a little more than our stable-comfort custom did, but that’s to be expected on a frame that is designed differently. This bike gives the stiffness of the BMC SLT01 or Colnago E-1 but does so with better comfort (not light praise as those are two very good bikes) and better stability that comes from being dead center on fit with a well matched fork. It’s dead on what I asked for with better comfort than I had thought it could have. It is as comfortable as lots of Ti that doesn’t have a prayer of being this stiff, and better comfort than some off the shelf Carbon focused on stiffness. Damn impressive.
That’s the Point!
It’s important to note that a great custom built bike will focus squarely on what you ask, but it will also let you sacrifice less in the areas it is not focused on. If I had wanted this to be a super laid back, longer wheel based, stable, comfort first bike, Seven could have handed be just that. It’s not all about stiffness or all about comfort, it’s all about you.
That’s the real value of custom done well as it considers Fit, but goes two steps further taking material choice as well as manipulation of that material into consideration. The highs are higher and the low’s less so.
Your bank account will get a little lower for a bike spec’d like this though. As built, if you could get zero Gravity to custom etch something and get Tiso to do one-off cranks direct from Italy, waited for Schmolke to get your other parts made to spec and shipped from Germany and then landed Reynolds and American Classics wheels, JagWire’s cables, a funky chain. You’ll be rolling around near 12 grand (shipping, customs and one off time come at a cost). But you can spec an Elium race built up for close to half that. The full custom frame and fork is $4,240. That’s near the top of anyone’s cost sheet, but the services that go in to that make the value relative. You can spend less on a frame just as easily as you can get less from it…
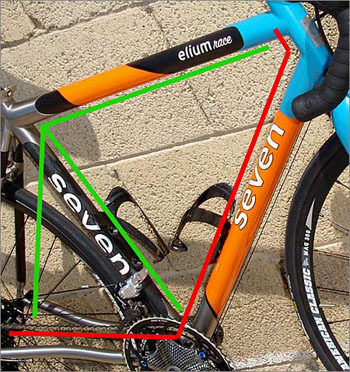
Fret not though if you’re looking for Seven’s custom service for less than something that usually comes with an engine. You can get something from them in the $1500 range (frame only) too and the value for custom at that price is extremely good.
Have At It
You can take a peak at Seven by heading to SevenCycles.com. They have dealer locators, company history and the full model line up there (including a slew of options and color schemes).
Also call the guys at Bicycle Ranch if you’re in the South West. They built this puppy and also handled the fit check.
Hit up CyclingInnovations.com for the super trick Tiso gear and ROI Zefiro carbon cranks. They also do OEM stuff for manufacturers and teams.
Schmolke Carbon are the Uber Masters of high end light. They will custom make seat posts (reinforced just at your specific seat height) and bars with a combination of weight and strength that I didn’t think existed. Bring your banker though.
Mean while, I will be busy explaining to the rest of the Pez staff that Seven’s motto is not “One Bike, Yours”. It’s One Bike:
Mine!
Note: if you have other experiences with gear, or something to add, drop us a line. We don’t claim to know everything (we just imply it at times). Give us a pat on the back if you like the reviews, or a slap in the head if you feel the need!