Few Framebuilders Have As Much Carbon Experience As Seven's Founding Team
Many riders think of Seven as a titanium framebuilder. However, Seven is also a carbon framebuilder.
Seven's founding team has been building with carbon for 38 years. We were involved in building some of the world's first and most influential carbon-metal frames. We hold patents for carbon framebuilding techniques and have carbon engineering, machining, and framebuilding experience that few others do.
We are unbiased about materials. We work with carbon fiber and titanium every day. No other builder has as many years of continuous carbon and titanium building time as Seven. We choose carbon for some applications and titanium for others. No material is perfect for everything.
Seven's Carbon Engineering Timeline
Here is a selected listing of our founding team's nearly four decades of carbon framebuilding experience.
The 1980s
Between 1987 and 1997, some of Seven's founding team worked at Merlin Metalworks, a titanium framebuilder and innovator.
In 1988, we worked with John Tomac and Mongoose on the world's first mountain bike frames incorporating carbon fiber.
In 1988, we worked on the world's first bladder-molded carbon mountain bike frame elements (with John Tomac and Mongoose). This gave us experience with molded carbon years before it became a standard carbon manufacturing method. We were also among the first to experiment with carbon-to-titanium bonding agents.
The 1990s
In 1990, we worked on the world's first titanium-carbon mix bikes. A project for John Tomac and Raleigh.
In 1990, we built the world's first titanium lugs for a ti-carbon frame. This was for John Tomac and Raleigh. We went on to machine and weld the titanium elements for their production model.
In 1990, we worked on the world's first carbon-wrapped aluminum tubed bonded and welded frame — for John Tomac and Raleigh.
In 1990, we welded the titanium elements for the world's first seven-carbon-tubed frame with titanium lugs. A project we did for Specialized. We went on to weld the titanium lugs for their early production bikes.
In 1991, Rob V. started running in-house fatigue tests of all kinds of materials and material joining techniques. We've done thousands of hours of carbon frame fatigue testing over the years.
In 1997, Rob V. designed and built the world's first carbon-titanium frame with strategic use of those materials: The Odonata. Rather than employing carbon in as much of the frame as possible (for marketing purposes) or carbon just where it's easy (for cost-saving purposes), we designed the frameset to leverage the best of both titanium and carbon.
In 1997, we started working with filament-wound carbon. We were among the first framebuilders to incorporate filament-wound tubing into a frame design; the Odonata.
We developed the world's first successful carbon-titanium bonding method that is still in use after nearly three decades. First used on the Odonata and continued today with our 622 and PRO bikes.
Beginning in the late 90s, Seven's lead engineer was sought after to consult for some of the most prestigious carbon framebuilders in the U.S.
The 2000s
In 2000, we introduced the world's first custom carbon fork. It is still the only carbon fork with over a dozen rake options.
From 2000 through the decade's end, Rob V. spent many months working in mainland China and Taiwan in dozens of carbon frame factories. Working on designs for Seven and as a consultant for other bike companies.
In 2001, Rob V. began a formalized in-house process for testing carbon frames of other manufacturers.
In 2002, we introduced the world's first mid-reach custom carbon fork.
In 2003, we built the world's first carbon-steel mixed material frames.
In 2003, we built the world's first full custom carbon bladder molded frames. These frames resemble monocoque frames with shaped tubes but offer fully customizable fit and handling geometry.
In 2005, we designed our in-house fatigue testing equipment for full frames and components. We've tested endless carbon frames over the years.
The 2010s To Today
In 2010 and 2011, Rob V. secured patents for custom carbon framebuilding tube joining techniques.
Today, we've built more custom carbon frames than any other builder. We've built thousands of frames with bladder-modeled carbon tubing. We've built thousands of frames with filament wound carbon tubing. We've consulted with some of the most prestigious carbon framebuilders. The list goes on. In summary, we have more diverse carbon experience than just about any custom builder.
Over the past 38 years, we've designed, built, and tested just about every iteration of carbon technology. We've chosen the methods that work best for building the highest-performing handbuilt framesets possible.
A Few Examples Of Carbon Projects
1990: World's First Titanium-Carbon Mix Bonded Frames
Original article with additional photos.
While working at Merlin Metalworks, our founding team had the good fortune to work on the first-ever titanium-carbon bonded frames. The Raleigh John Tomac Signature.
This is a carbon fiber-wrapped aluminum tube titanium lugged mountain bike frame. John Tomac raced these bikes to numerous wins in 1990, 1991, and 1992.
We had worked with Tomac three times previously: On a titanium frame[1], a titanium-steel frame[2], and another carbon-titanium race bike project[3]. (All stories for another time.) Because of that experience and bike performance, Tomac told Raleigh that he would only race for them if Merlin built the frames[4].
This frame consists of a titanium head tube lug, titanium rear triangle with seat cluster lug, and bottom bracket lug. We did all of the titanium machining and welding. The top tube, down tube, and seat tube are carbon-wrapped aluminum tubes. Nothing like it had ever been done before. There were at least a few firsts happening with this production frame:
- World's first carbon-titanium frame (not including Merlin's previous project that included bladder molded carbon).[3]
- World's first titanium-lugged frame of any kind.
- World's first bonded mountain bike frame of any kind.
- Worlds first carbon-wrapped aluminum tubes employed in a mountain bike frame.
- Worlds first frame to include both internal and external lug connections. The seat tube cluster is internal. The other lugs are external.
We machined and welded all of the prototypes, John's race frames, and the production frames for about two years. To our knowledge, not a single one ever broke, unbonded, or failed in any way.
Seven Cycles employees who were at Merlin and worked on the Tomac-Raleigh frames included Tim Delaney and Rob Vandermark, who welded all of the prototypes and production frames. Matt O'Keefe and Skip Brown did a lot of the machining. Jennifer Miller worked on sourcing and making sure we got the job done.
Tomac went on to win countless races on this bike, including the 1991 Grundig World Cup Championship, the 1991 Mountain Bike World Cross-Country Championship, and the 1991 NORBA National Championship Series.[6]
We were fortunate to work for John Tomac for over 5 years, from 1988 through 1992. One of the greats.
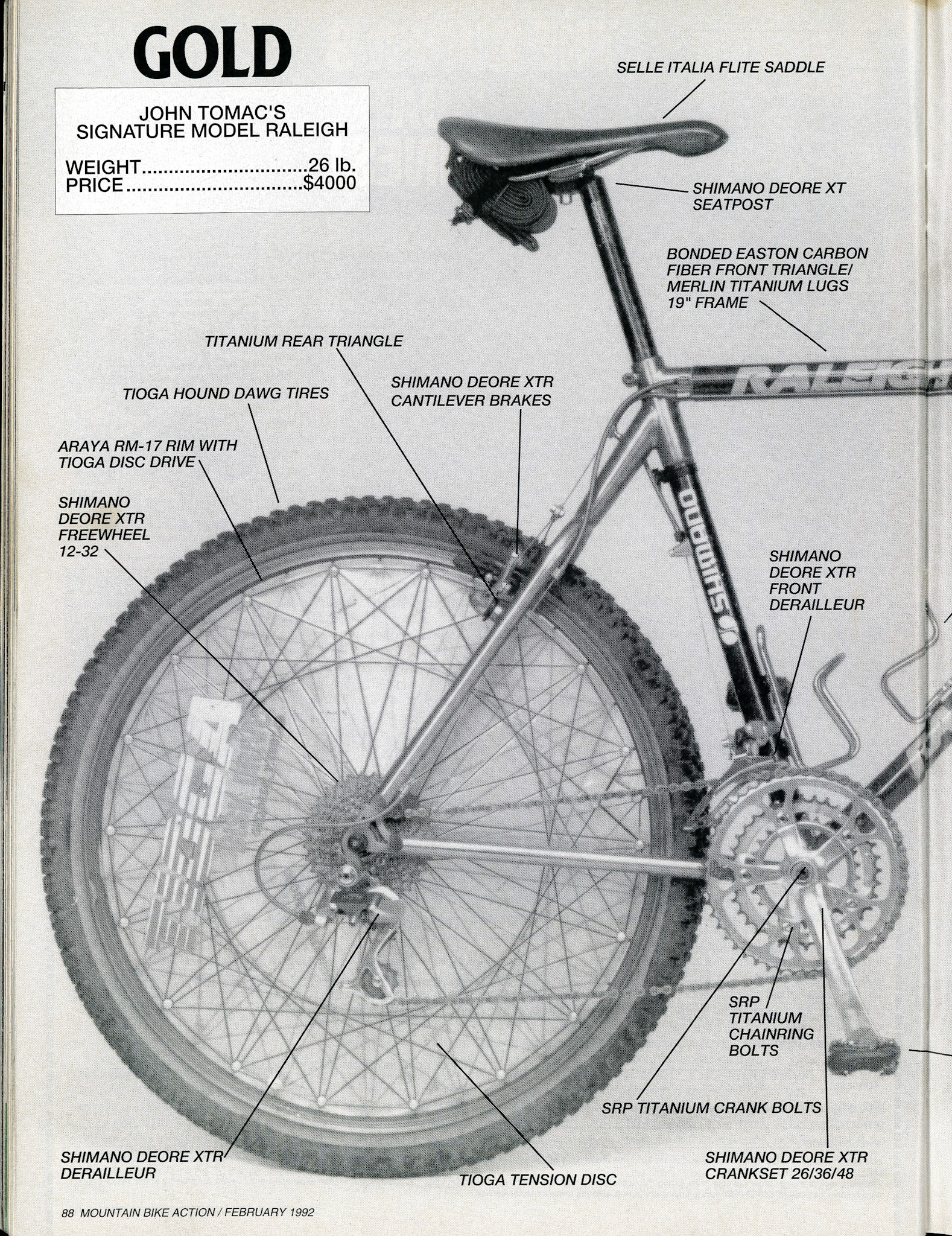
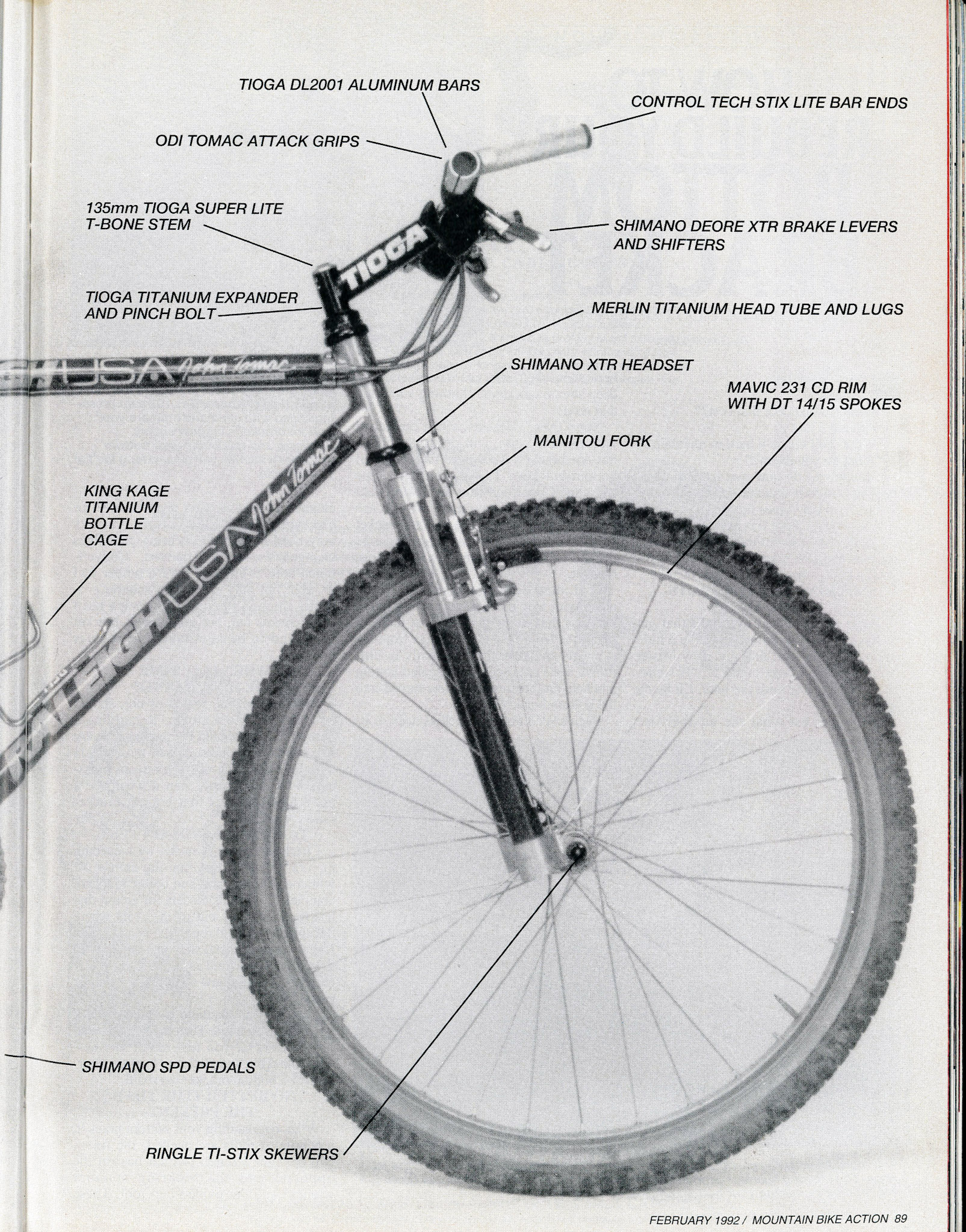
Raleigh-Tomac Footnotes:
- ^ Mongoose titanium frames for John Tomac.
- ^ Mongoose Titanium Signature, John Tomac (titanium front end and steel rear end — seat stays, dropouts, chainstays).
- ^ A titanium-carbon composite that John Tomac raced for Mongoose but was never released as a production offering.
- ^Source: Conversation with Matt O'Keefe.
- ^ A titanium-carbon composite that John Tomac raced for Mongoose but was never released as a production offering.
- ^ Wikipedia.
1990: World's First Titanium-Carbon Mix Frames With Full Carbon Tubes
The Specialized Epic Ultimate frames designed by Jim Merz.
At Merlin Metalworks, Seven's co-founders welded the titanium lugs for the prototypes, Ned Overend's race bikes, Mike Sinyard's bike (Specialized's founder), and the production frames.
Aptly named the Epic Ultimate, Ned Overend rode the bike to countless wins starting in 1991. (He also raced the Specialized M2 during this time, and it is unclear which bike he raced to which wins.) In 1991 and 1992, his accolades include the NORBA Mountain Biking National Champion, winner of the 1991 Park City UCI World Cup, winner of the 1992 UCI World Cup Finals, winner of the 1992 UCI Mammoth World Cup, and winner of the 1992 NORBA Point Series. He took bronze in the 1992 UCI World Mountain Bike Championships.[2][3]
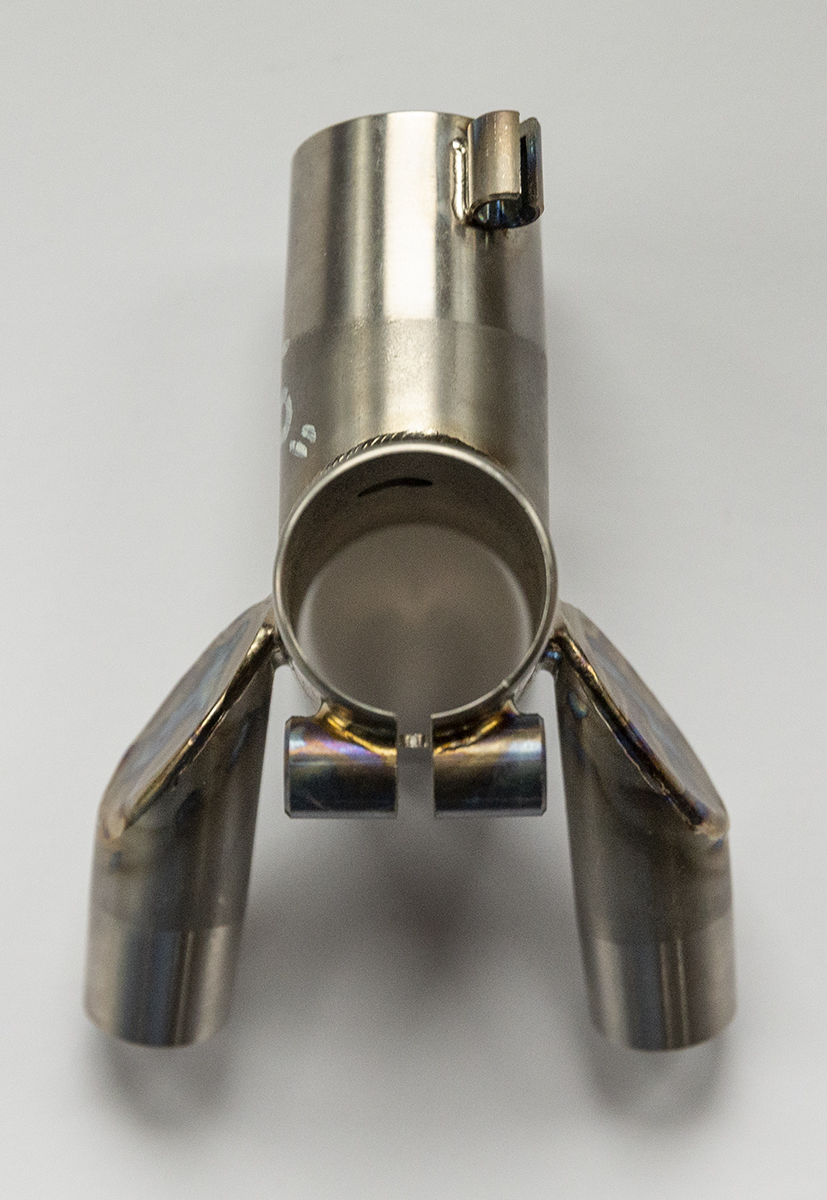
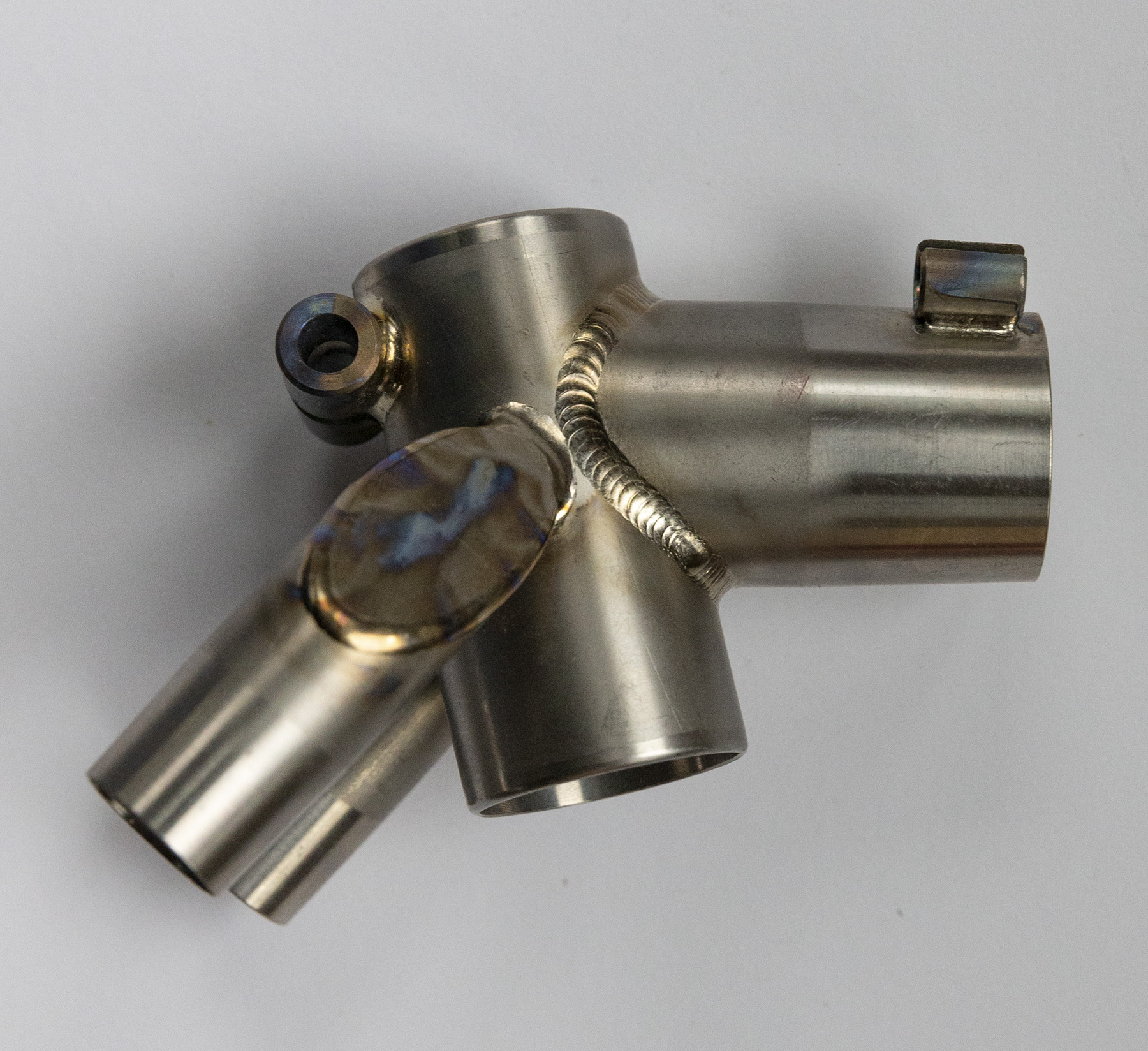
Source 2: U.S. Bicycling Hall of Fame.
Source 3: Wikipedia.
1997: World's First Strategic Application Of Carbon
Seven's Odonata was the first mixed material frame to employ carbon for rider performance and strategic purposes. Most carbon-mix frames of the time applied carbon in all tubes or for marketing-cost-savings purposes. Seven carbon-titanium frames applied carbon where it would be most beneficial to the ride and performance of the bike.
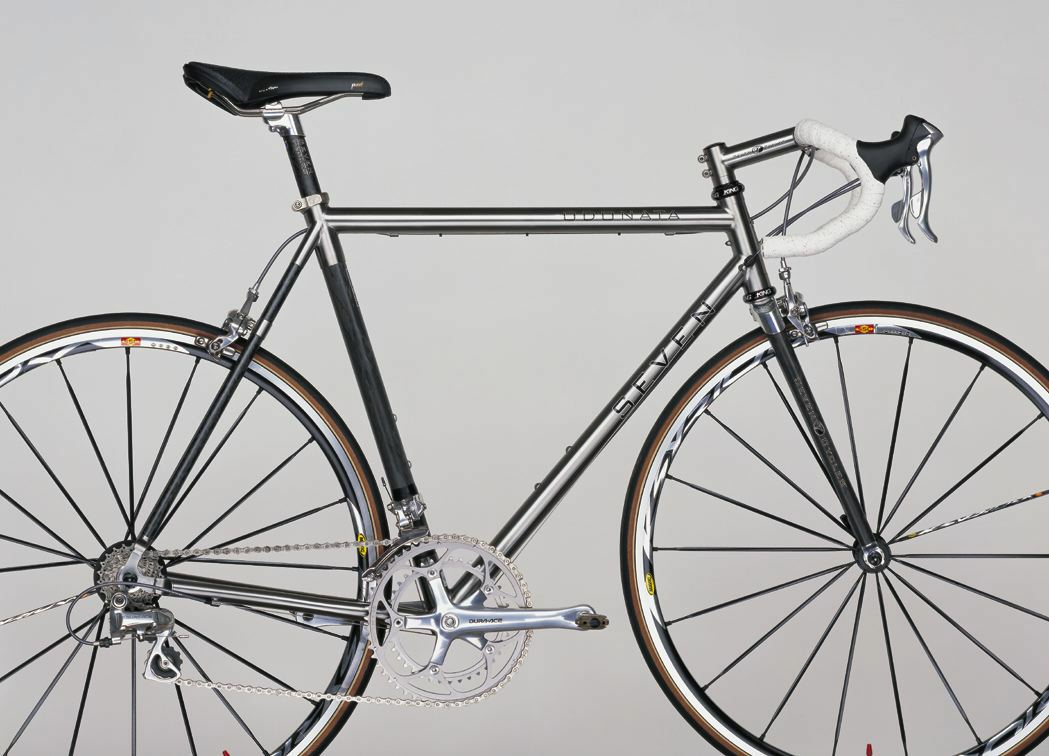
2005: World's First Patented Full-Carbon Full-Custom Monocoque-Style Frame
Seven's A6 carbon frame chassis pushed the technology of the time. So much so that we were granted patents for the process. We offered a series of road and triathlon bikes.
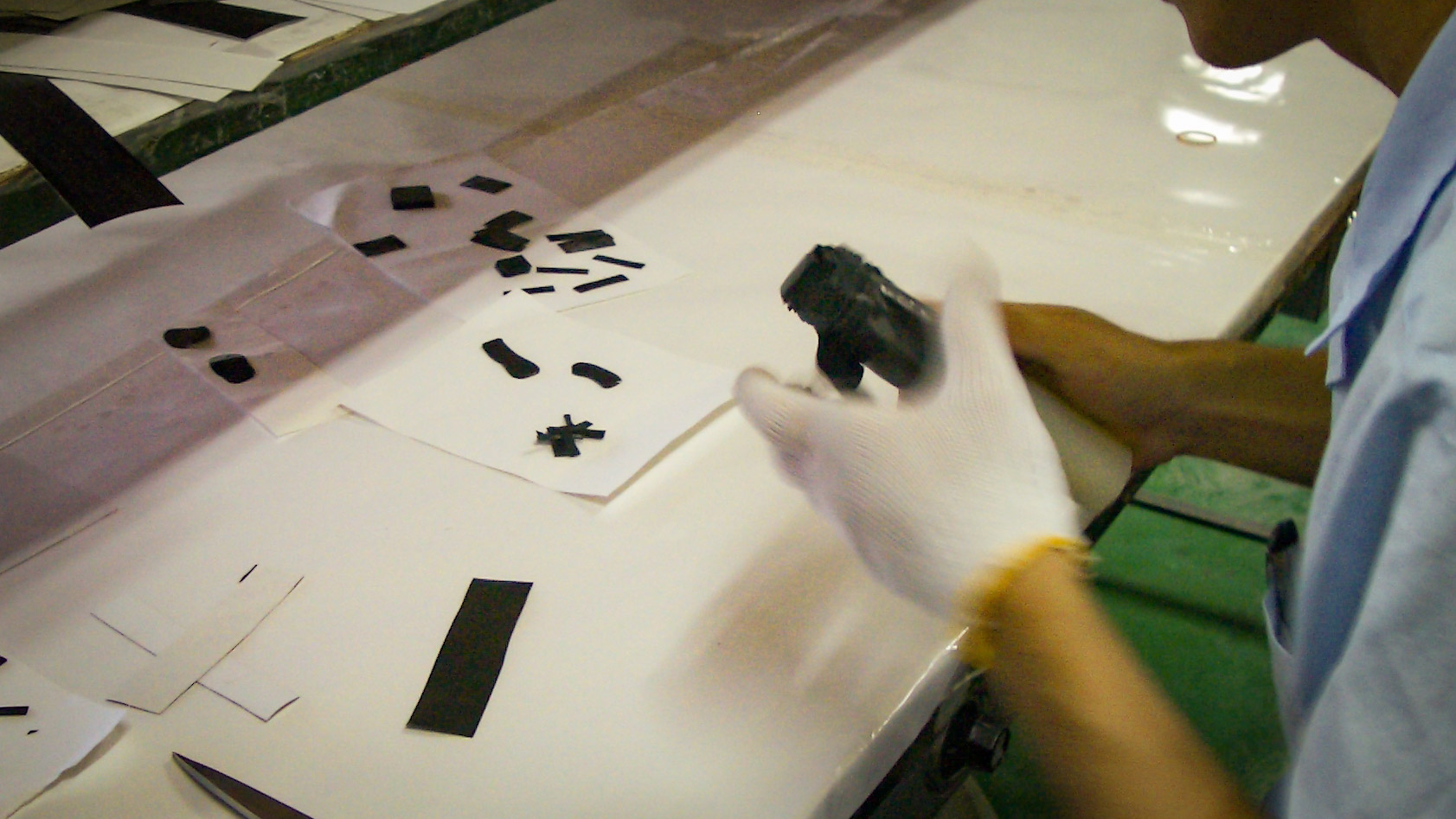
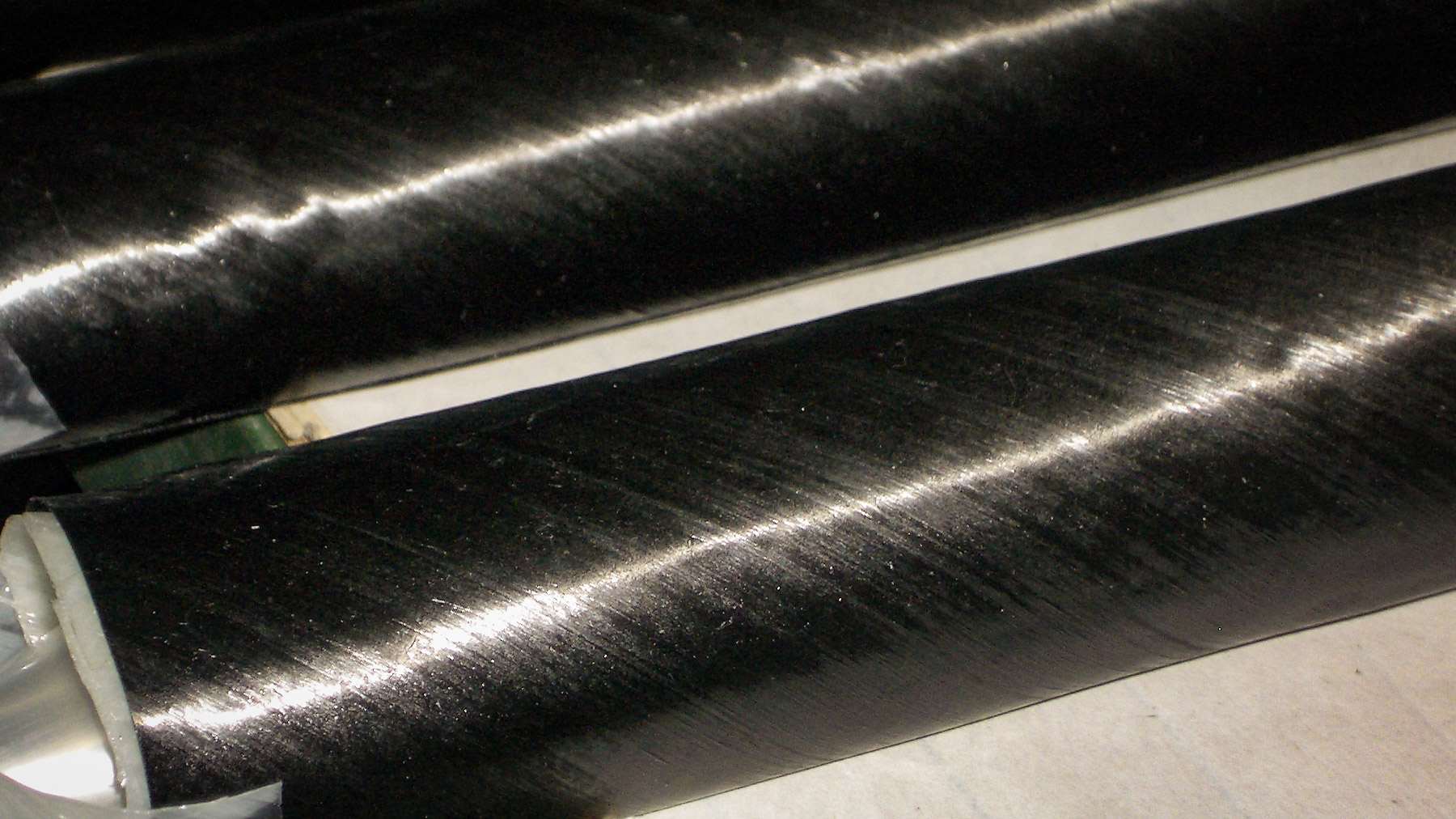
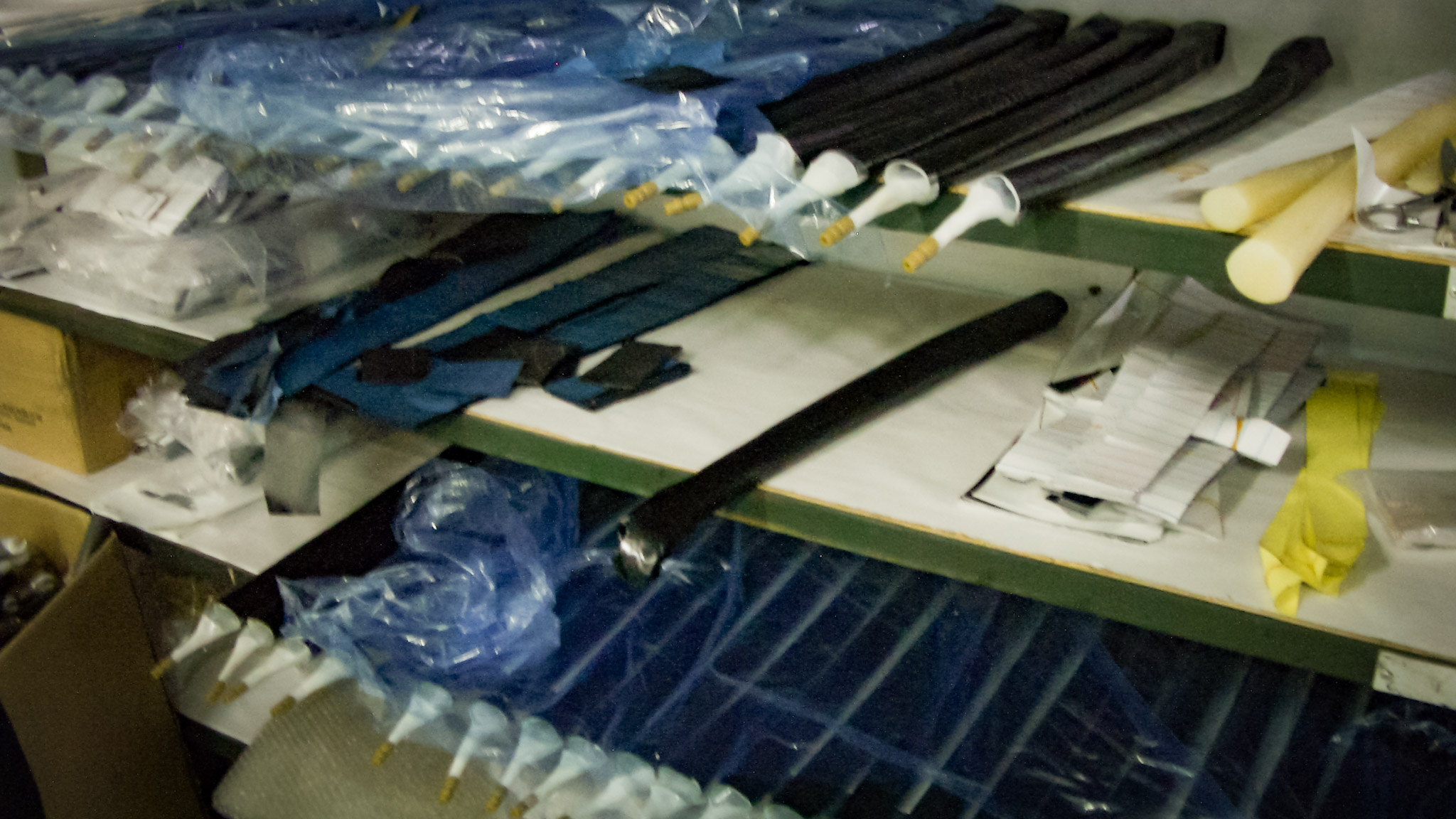
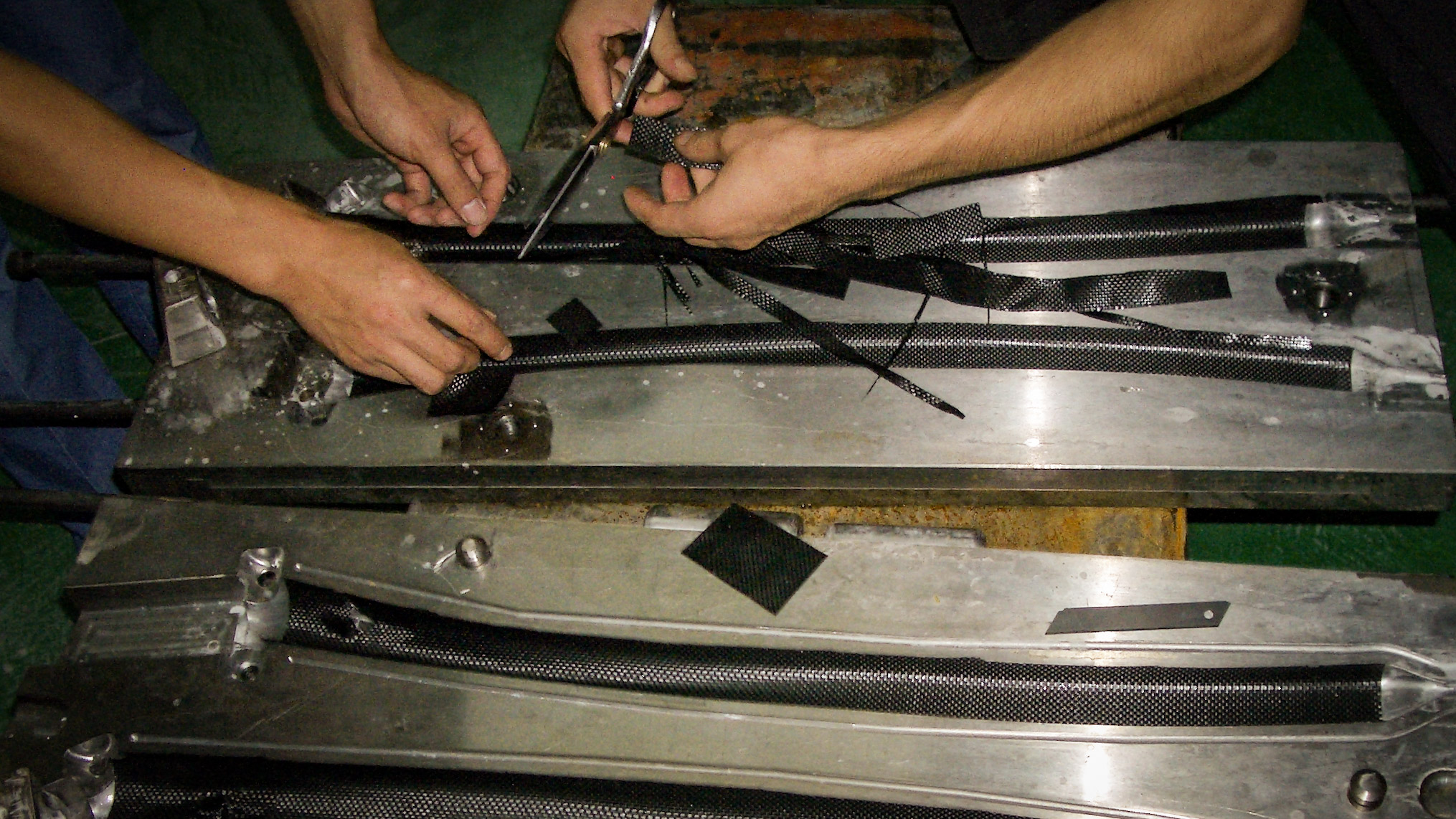
Today: Continuously Improving The Process
We build each carbon frame one at a time in our Massachusetts factory. Each frame is built to order by what is likely the most experienced team of framebuilders on the planet.

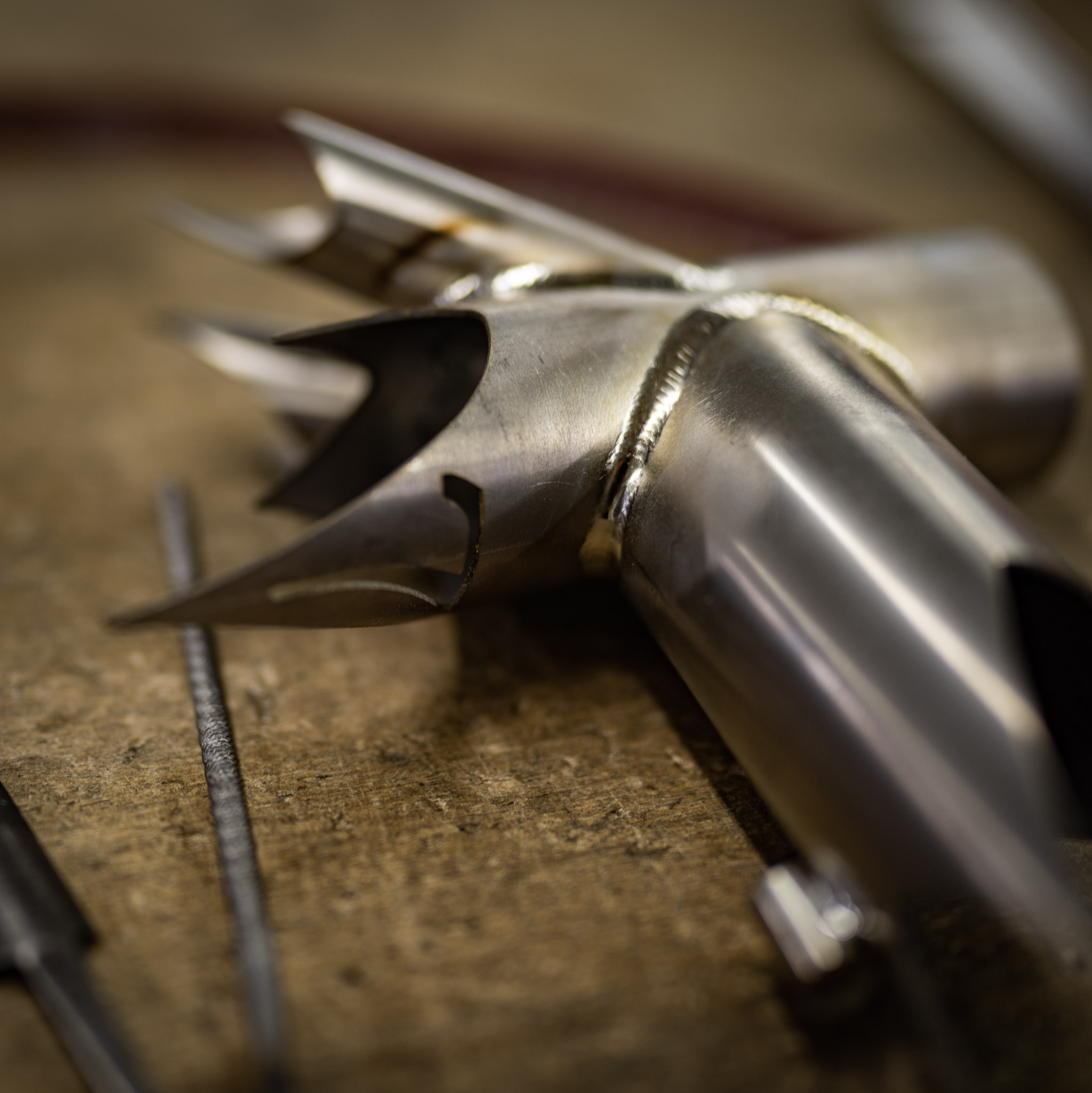
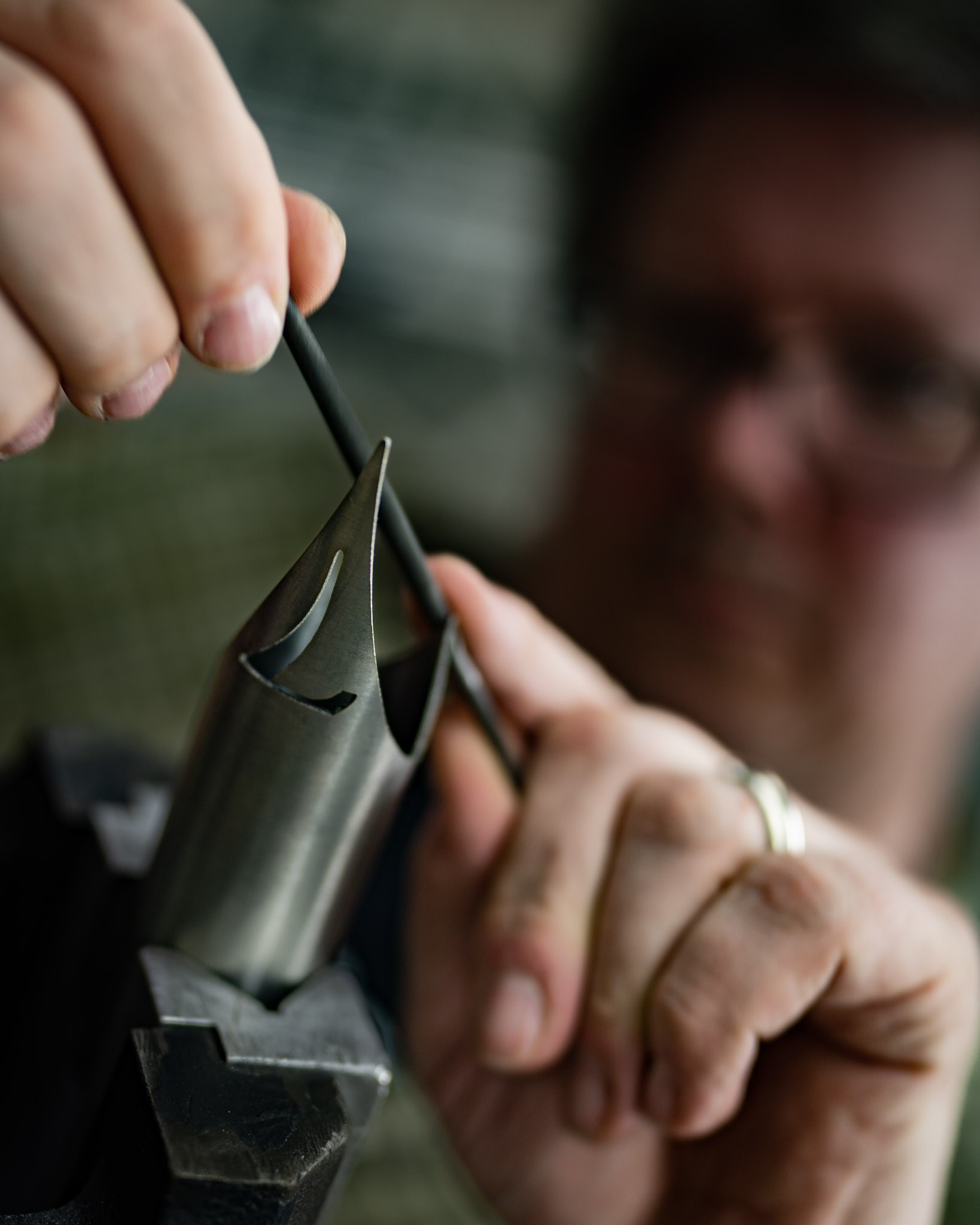
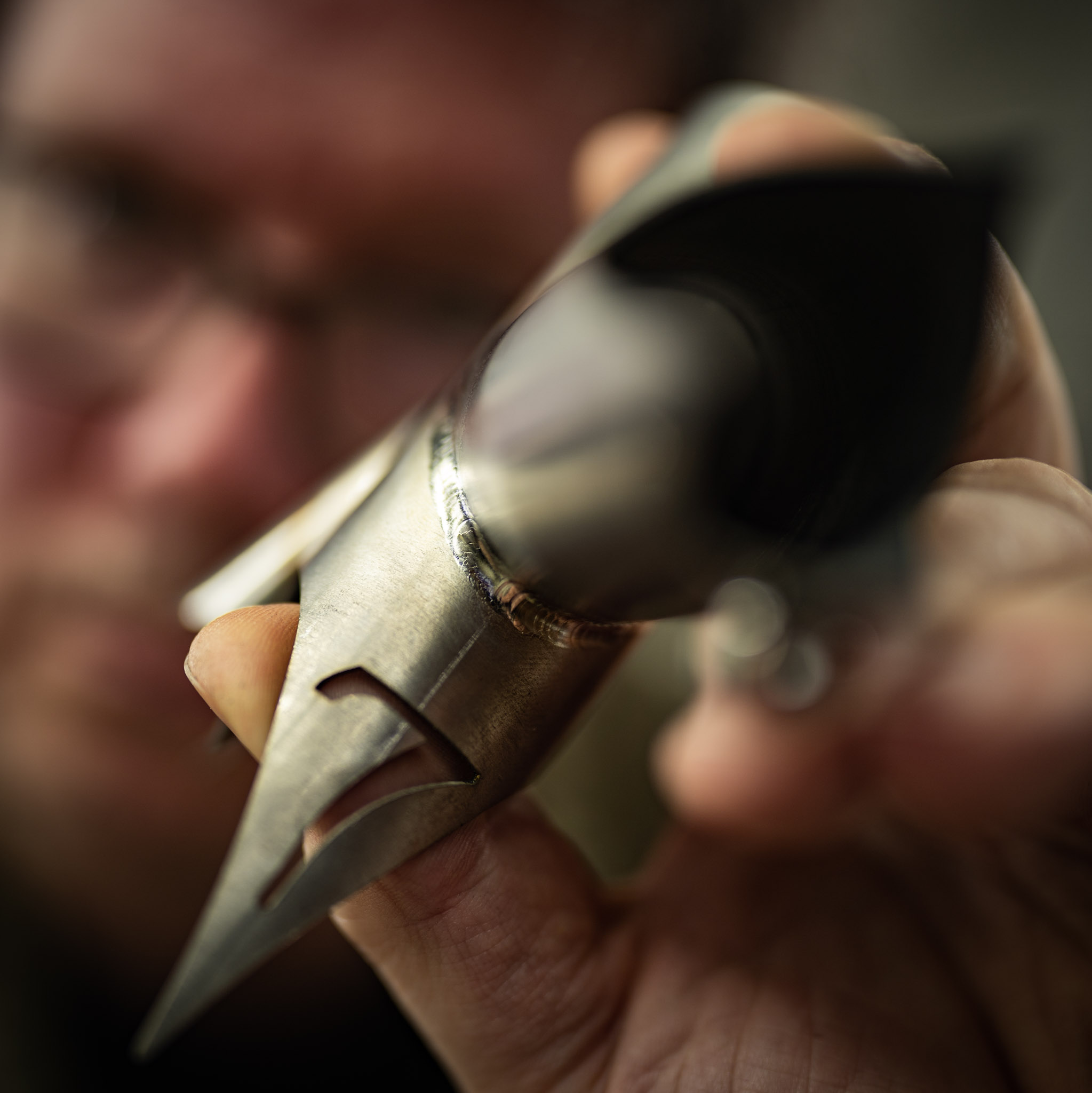
Seven's In-House Fatigue Testing Machine
Rob V. began fatigue testing materials and joining techniques in 1991 and has continued since. In 2005, we designed our own full frame and component fatigue testing machine. Over the past two decades, it's seen a lot of wear and tear.
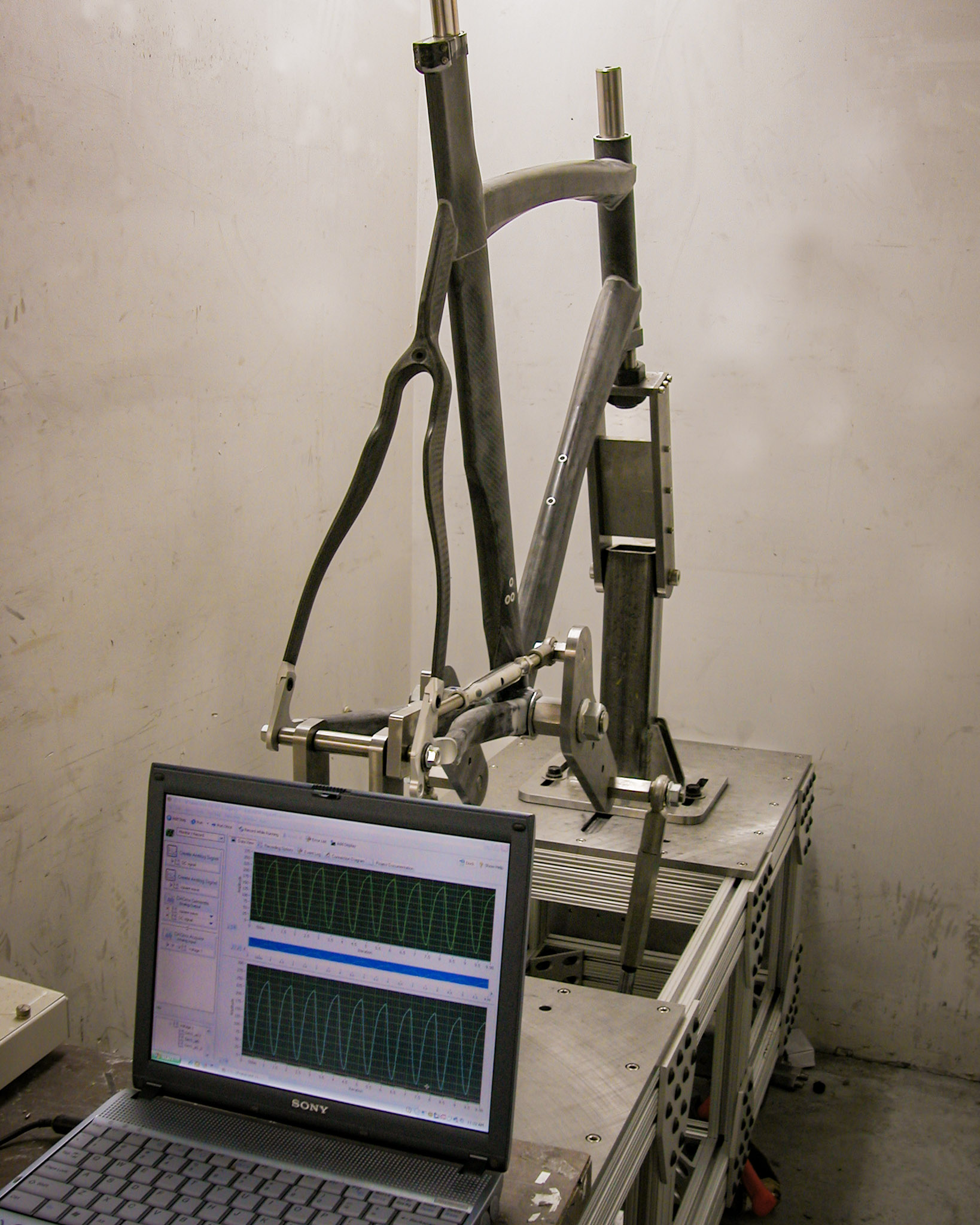