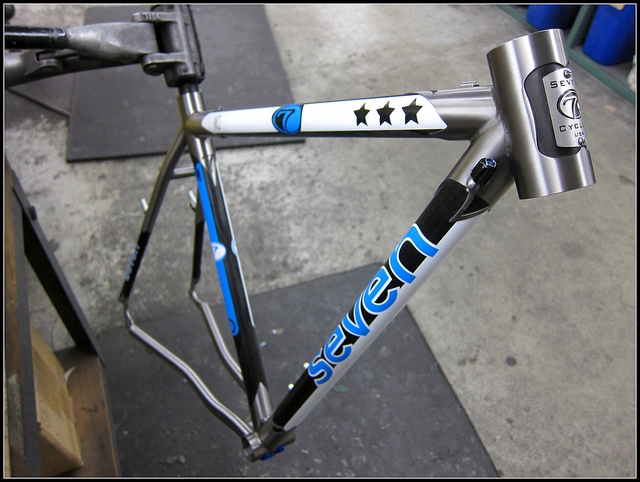
A few weeks ago, Mo Bruno Roy returned her original Mudhoney PRO prototype. Affectionately called the Mo Honey PRO, that bike was the test case for the bike that became the production Mudhoney PRO, the bike that customers all over the world have ridden over the last season. Mo’s original was put together with hand cut and filed lugs, and she raced it hard this season so we could know more about our basic design assumptions, and to gather experiential data for the second iteration, Mo Pro 2.0, of this race-specific machine.
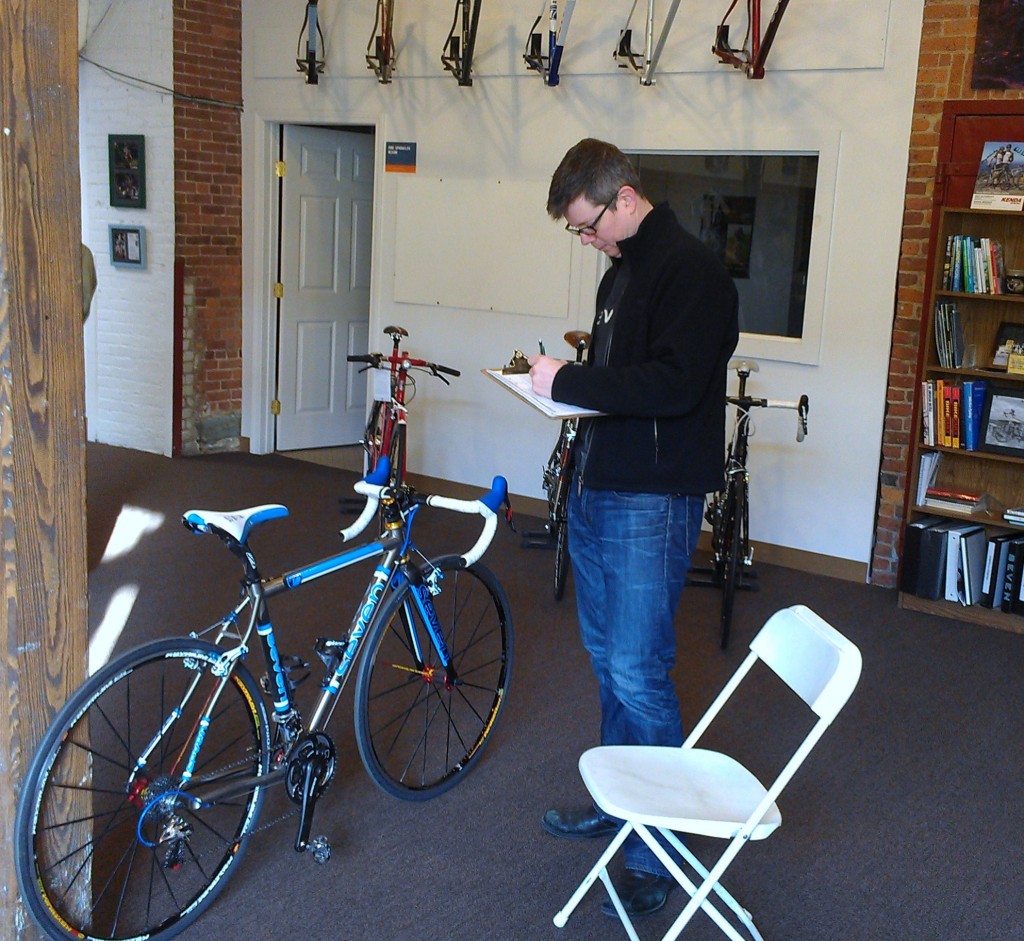
During our debrief with her, and with her mechanic/husband Matt Roy, we noted a few big, necessary changes. First, Mo wanted to change her riding position. She wanted to come forward, and up a little. To do that, she needed to make some component changes, and to maintain the handling she prefers after those changes, we needed to adjust the geometry. Easy enough.
Next, she wanted more tire clearance at the chain and seat stays. The original prototype was built with tight tolerances for racing, but we learned that just a little more mud clearance would be better. That presented a unique challenge, because Mo’s frame is small. In order to get the clearance she wanted, we experimented with a single-bend, butted seat stay designed specifically for carbon bonding. That little bit of bend gave us just what we were looking for, and it represented a step forward for the super thin stays we’ve been working with for Mo’s race bikes. The complimentary chain stays required 20 separate operations in initial machining. This is serious stuff.
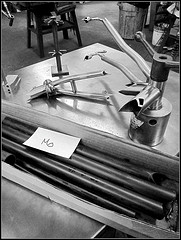
In the past, we’ve built bikes for Mo that could be adapted to multiple purposes. A little attention from her pro mechanic husband would convert one of her race rigs for road training. Not this bike. Mo runs a somewhat unique crank set with 34/44 chain rings, and her seat/chain stays are optimized to work only with those rings, coupled with a 32mm tire. This is as race specific as a bike gets. It’s a bike for now, for winning races.
We opted to build for cantilever brakes, too, but only because race ready, drop bar, hydraulic disc brakes aren’t quite ready yet. Again, we wanted to build her the optimal race bike for right now, not a bike with compromises for future adaptation.
The final design hurdle we chose to address was toe overlap. Conventionally, a frame this small would have some overlap, and through the years, this was always something Mo was comfortable with, even though we offered to do away with it for her. This time out, we made some adjustments to the geometry to eliminate it, and that gives her more confidence in the technical sections of the cyclocross courses this bike was meant to destroy.
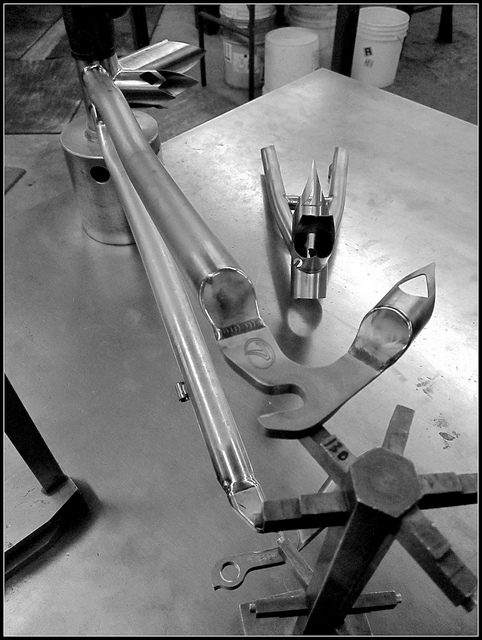
A lot of work went into pre-build design on the Mo Pro 2.0, and that led to a marathon build session that lasted long into the Friday night before Mo’s first race on it, on the Saturday. Seven Production Manager Matt O’Keefe did the final machining on this one himself, before handing it off to Staci for the rock star decal treatment.
As ever, our sponsorships are aimed at exactly this sort of collaboration. We built the original bikes to prove a concept we wanted to bring into production. After building the first generation prototypes, we then designed all the fixturing we would need to do the same design for customer bikes. In turn, the fixturing informed the accuracy and evolution of the second generation bike, which taught us about new ways to manipulate thin stays for small builds. It’s this thread that connects all our design and build work and allows everything to move forward, and to be able to pursue that thread with the input and participation of pros like Mo and Matt makes bike building fun. It reminds us why we do this.
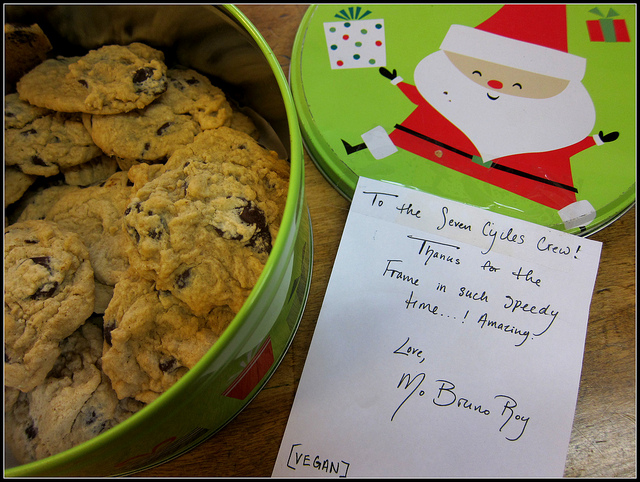
Another solid reminder came in a Christmas tin a few days later. Her feedback on the bike itself is exactly what we wanted to hear, that it combines the best of her first Seven race bike and the first generation Mo Honey PRO. That confirms that we’re listening, and without listening you can’t build great custom bikes. It doesn’t matter whether you’re building for a pro like Mo or someone who will never race a day in their lives. The process is the same. Listen to what the rider wants. Apply everything you learn to everything new you want to do. Keep building. Keep iterating. Occasionally, just occasionally, stop to eat the cookies.
Matt made a cool time lapse video of the build that you can see here:
Project Codename: #MoPRO2 from Matt Roy on Vimeo.
And we were also fortunate to catch the eye of the Velo News staff at our very first race. Emily Zinn did a photo gallery of the project for their site.