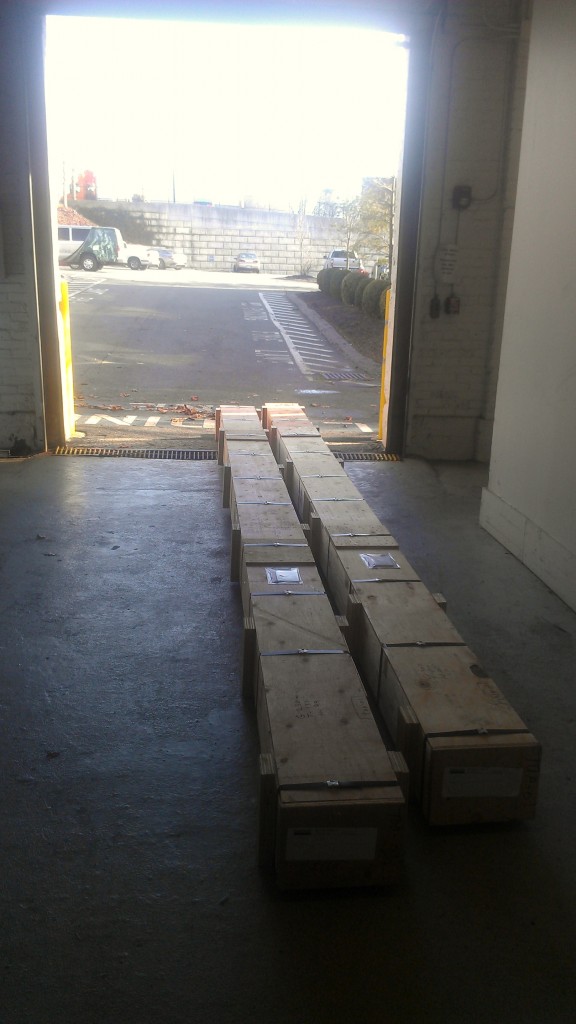
Every few weeks a freight truck wends its way down our steep, angled driveway to drop off two or three of these long wooden boxes. They contain raw titanium tubing in 18 foot lengths, all different gauges. The process of loading the unwieldy boxes onto a four-wheeler and moving them past the shipping department, through paint and into the machining area, one at a time, is something like a tugboat pushing a long cargo barge up the narrow, jagged length of the Mississippi River. It takes a strong sense of spatial relations and a fair amount of experience.
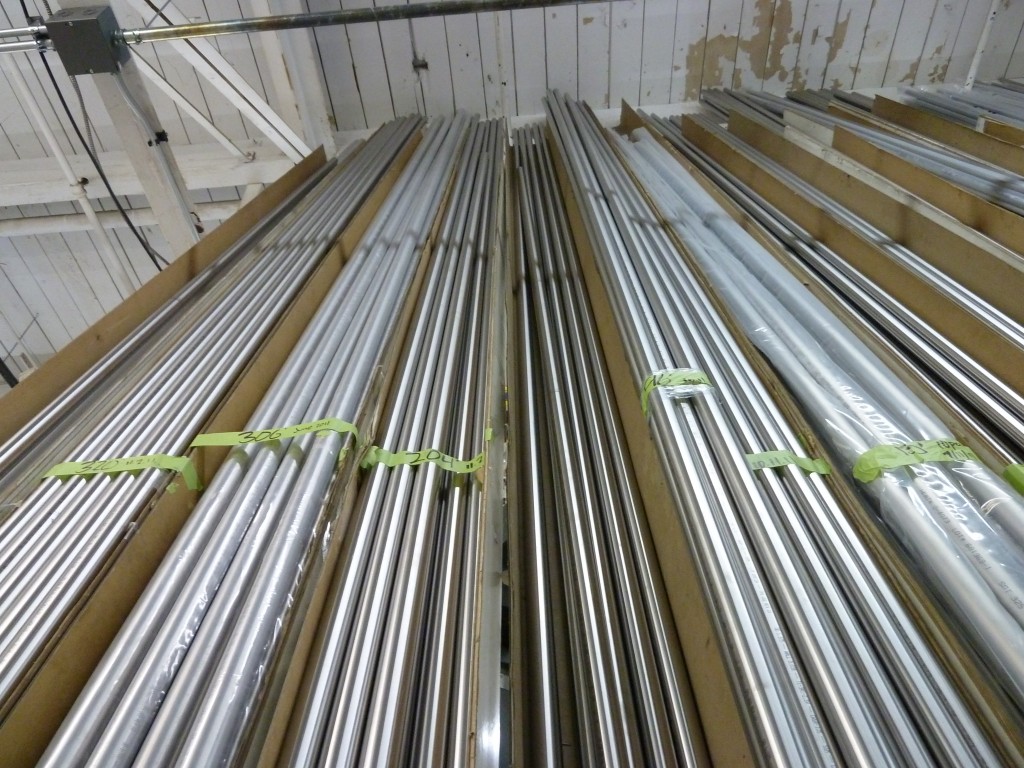
The boxes get unpacked and the various tubes sorted by size into these vertical bays. This is our vault. This is our wine cellar. This is where the process of building a new bike begins, Matt O’Keefe standing here in front of the stock, a customer’s order in his hands, selecting the assortment of tubes that will go into their new bike.
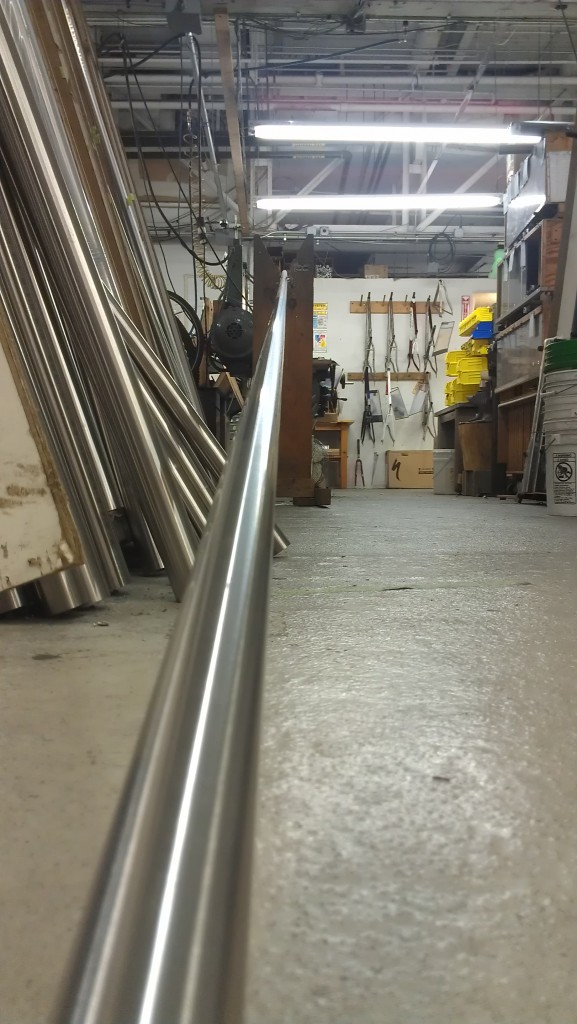
We cut down the lengths to size, before butting each tube to give a very specific ride feel and handling characteristic. Then we miter the ends to fit together just so, tolerances hovering somewhere near the thickness of a human hair, the raw tubing shedding material in small increments, becoming a bike.
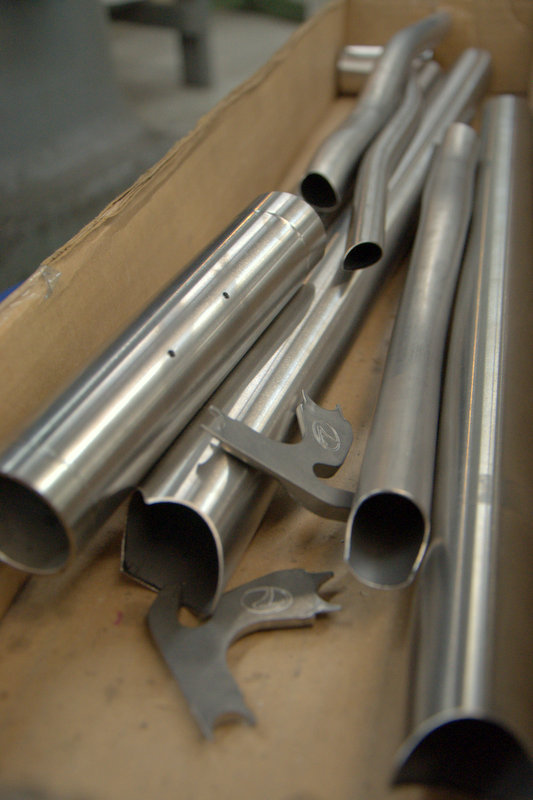
The modified tubes collect in small cardboard boxes, the frame builder working through a series of work cells, each with several mills or lathes in it, each set up for a very specific job, until the tubeset is complete. Then they get jigged up, so we can test the build against the frame drawing, refine any last details.
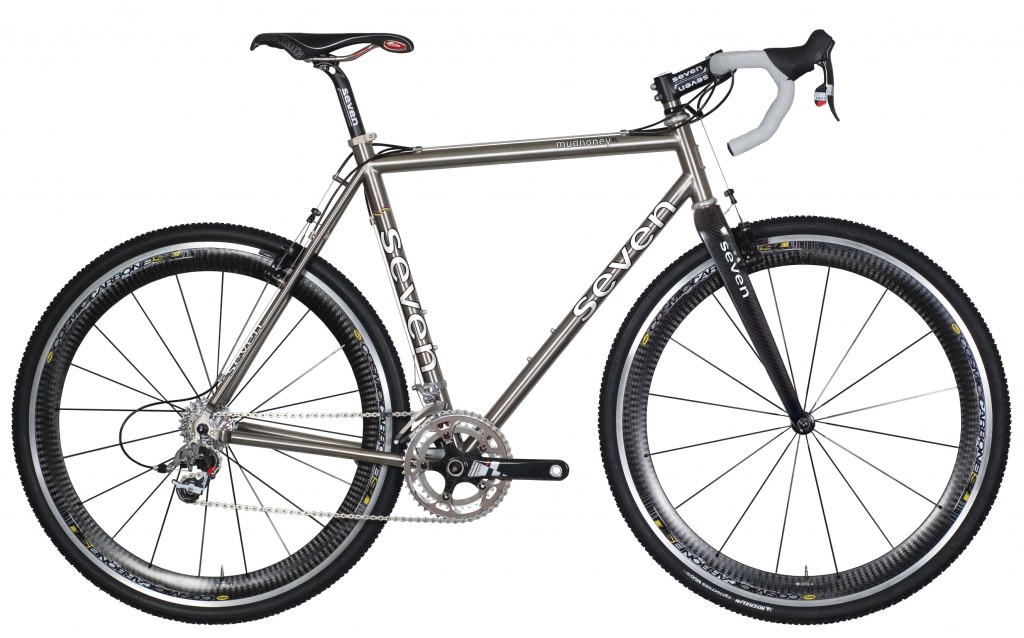
Eventually, you get one of these. There are, as you can imagine, some important intervening steps, but this is the abridged version of the story. Suffice it to say we weld, machine, finish, polish and decal, before we get to this point. Sometimes we paint.
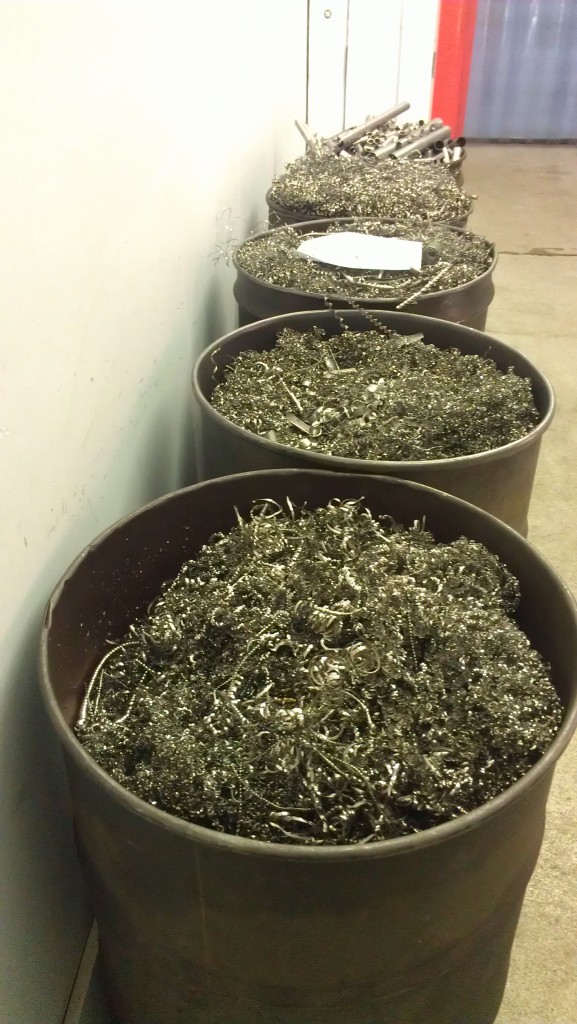
What titanium doesn’t make it into the frame gets carefully collected in a barrel, building up over time into a strangely beautiful pile of titanium squiggles and spirals. The recycler comes by to pick these up and return them to the mill where the process starts all over, a closed loop of magic from which we extract custom bicycles.
The end..